2024年03月01日
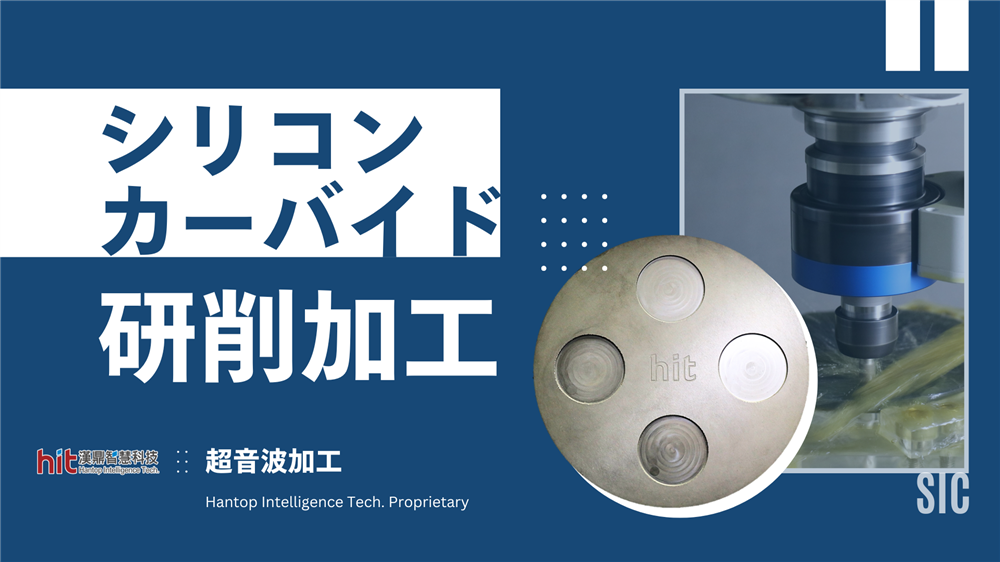
超音波研削 SiC(シリコンカーバイド)ウエハ製造の世界を変える利点
SiC(シリコンカーバイド)およびその半導体製造プロセスでの一般的な使用について
SiC(シリコンカーバイド)の材料特性
SiC(シリコンカーバイド)は、半導体および電気自動車の重要性の急速な上昇により、近年非常に人気のある材料となっています。材料の特性は異なる形成方法によって異なる場合があります。以下はシリコンカーバイドのいくつかの典型的な材料特性です:
【高い硬度と良好な機械的強度】
SiC(シリコンカーバイド)は非常に硬い材料であり、モース硬度スケールでダイヤモンドに近いランク(モース硬度評価で9)です。この硬度により、摩耗に強く、したがって良好な機械的強度を持っています。これは、機械的負荷と応力に耐える高精度な機械部品にとって優れた材料選択となります。
【優れた熱伝導性と安定性】
SiCは非常に高い融点(約2,700℃または4,892°F)を持ち、熱ショックに強いです。この特性により、酸化および腐食性の環境でも高温下でその構造安定性を維持できます。材料は優れた熱伝導性を示し、効果的な熱伝導体となっています。
【電気伝導性】
SiCはその結晶構造によって半導体または導体となります。この材料は、広いバンドギャップ(WBG)を持つため、電力エレクトロニクスおよび高周波RFデバイスにとって価値があります。半導体材料のバンドギャップは、電子を伝導帯に移動させるのに必要なエネルギー量を決定し、導体として機能します。従来、シリコンは主に半導体に使用されてきました。広いバンドギャップ材料として、SiCは同じ電圧を維持するためにシリコンよりも薄くなる可能性があります。これにより、シリコンベースのデバイスと比較して導電およびスイッチング損失が低減します。
SiC(シリコンカーバイド)の半導体ウエハファウンドリプロセスでの一般的な使用
半導体製造チャンバー内の主要な予備部品はSiC製であり、ウエハファウンドリプロセスのさまざまなアプリケーションに不可欠です。重要なSiC予備部品の一部には以下があります:
【SiCウエハ基板およびウエハサセプター】
SiCウエハ基板は、他の半導体材料(ガリウム窒化物など)のエピタキシャル成長の基盤となります。これらの基板は、高性能かつ高周波の電子デバイスの製造に不可欠です。SiCコーティングされたサセプターは、化学気相成長(CVD)およびエピタキシャル成長プロセスで使用されます。これらは高温および腐食性の環境に耐えつつ、薄膜とエピタキシャル層の成長をサポートします。
【SiCエッチングチャンバーおよびシャワーヘッド】
SiCはプラズマエッチングや化学気相成長などのプロセスのためにエッチングチャンバーとその構成要素(シャワーヘッドなど)を製造するために使用されます。優れた熱的安定性と耐食性の特性により、SiCはこれらのアプリケーションに耐久性のある選択肢となります。
【SiCベアリングおよびシール】
半導体製造装置では、SiCベアリングおよびシールが優れた耐摩耗性、熱的安定性、および化学的不活性のために使用されます。これらの材料特性は処理チャンバーや真空環境の完全性と安定性を維持するのに役立ちます。
【SiCセラミックノズルおよびプロセスチャンバー内のウェットクリーニング用ライナー】
SiCノズルおよびライナーは、プラズマエッチングやウェットクリーニングプロセスで使用されます。これらのプロセスでは、高温下で侵食性および腐食性のある化学薬品が関与します。SiCの化学耐性と熱的安定性の材料特性は、この文脈で有利です。
SiC(シリコンカーバイド)研削のメカニズム
研削の初期段階では、研削工具の砥粒がSiCワークピースの表面に突き刺さり、溝や傷を作り出します。これは主に砥粒の硬度とワークピースとの接触に起因しています。
研削が進むにつれて、砥粒はSiC材料に切り込み始めます。この切削作用が材料の除去と所望の形状および表面仕上げの生成に貢献しています。一部のSiC材料は研削中に生成される高い応力と圧力の下で破壊される可能性があります。これにより微細なクラックが形成され、材料の除去に寄与することがあります。
SiC(シリコンカーバイド)研削の難しさ
SiCを研削することは、その独特な材料および機械的特性のために困難を伴うことがあります。SiC研削に関連するいくつかの難しさには次のようなものがあります:
硬度と脆弱
SiCは非常に硬い材料で、モース硬度スケールで9にランク付けされています(ダイヤモンドに近い)。この硬度は研削ツール/ホイールの過度な摩耗と急速な劣化を引き起こす可能性があります。また、SiC材料は非常に脆いため、研削中に破壊されやすいです。増加する研削力は、材料内の欠けやエッジクラックを引き起こし、仕上がり表面の品質に影響を与える可能性があります。
高摩擦と研削力の増加
研削ツールとSiCワークピースとの間の高い摩擦は、主に砥粒間のポア(SiC材料の残渣)にセラミック粒子(SiC材料の残渣)が蓄積されることから生じます。セラミック粒子の不良な排除は、ツールの研削能力の低下を引き起こし、それにより研削力の増加をもたらします。
ツールの摩耗とツールのドレッシング
SiCを研削するための研削ツール/ホイールは、粒子の不良な排除による研削能力の急激な喪失により非常に早く摩耗する可能性があり、頻繁な交換が必要となり、研削プロセスのコストが増加します。砥粒がSiC材料の残渣でロードされることを防ぎ、ツール/ホイールの鋭さを維持するためには、研削ツール/ホイールを定期的にドレッシングする必要があります。ただし、通常のツールドレッシングは大量のプロセス時間を取ることがあり、ツールドレッシングプロセス中にツールが追加の摩耗を受ける可能性があります。これは時間のかかるだけでなく、ツールの研削能力の急激な低下につながる可能性があります。
HIT超音波加工技術がSiC(シリコンカーバイド)研削にもたらすものは何ですか?
超音波高周波振動
HITの超音波支援加工技術は、ツールの回転に縦方向の高周波振動を重ね合わせ、毎秒20,000回以上の微振動を生成します。このメカニズムは研削力を軽減し、セラミック粒子のフラッシュを助けます。
縦方向の高周波振動により、ツールとワークピースの間に断続的な接触が可能となります。これにより、研削ツール周りの蓄積された熱が減少し、ツールの摩耗が大幅に軽減されます。
研削力の低減
研削力の低減は、ツールとワークピースの摩擦を減少させるだけでなく、切削速度と送り速度を増加させることが可能です。このメカニズムはまた、加工プロセス中に生成される熱を低減させます。これにより、ワークピースの品質とツール寿命の安定性が大幅に向上し、膨大なエネルギーと全体のプロセス時間が節約されます。
より良い粒子フラッシュ
セラミック粒子のフラッシュを促進することで、研削ツール/ホイールに付着した過剰な粒子によるツールとワークピースの摩擦も軽減されます。もし研削ツールの孔(砥粒間)が蓄積されたセラミック粒子で満たされていると、ツールはすぐに研削能力を失います。
超音波の高周波微振動により、より良い粒子フラッシュが生まれ、これが研削ツール/ホイールの自己研磨メカニズム(摩耗した砥粒が剥がれ落ち、新しいダイヤモンド砥粒が続けて研削)を助けます。これにより、ツールドレッシングプロセスからの時間とツール摩耗が大幅に削減されます。
HIT超音波技術のSiC(シリコンカーバイド)研削における利点
SiC(シリコンカーバイド)の研削において、HITの超音波支援加工技術は研削力を軽減し、より効果的な粒子のフラッシュをもたらします。このメカニズムにより、プロセス時間が大幅に短縮されます(ツールドレッシングプロセスの除去)、ワークピースの品質が向上します(エッジクラックの減少と表面品質の向上)、そしてツール寿命が延びます(ツールドレッシングプロセスの除去とセラミック粒子の蓄積の防止)。
💡 HIT 超音波加工技術の利点に関する詳細はこちら
💡 先進材料の超音波加工の利点:
-
漢鼎智慧科技 Hantop Intelligence Tech.
✨先進的な材料加工とスマート自動化ソリューションモジュール✨
☎️ +886-4-2285-0838
📧 sales@hit-tw.com
当社は、加工効率、品質、ツール寿命を向上させるより良い方法をお探しの場合、お気軽にお問い合わせください。