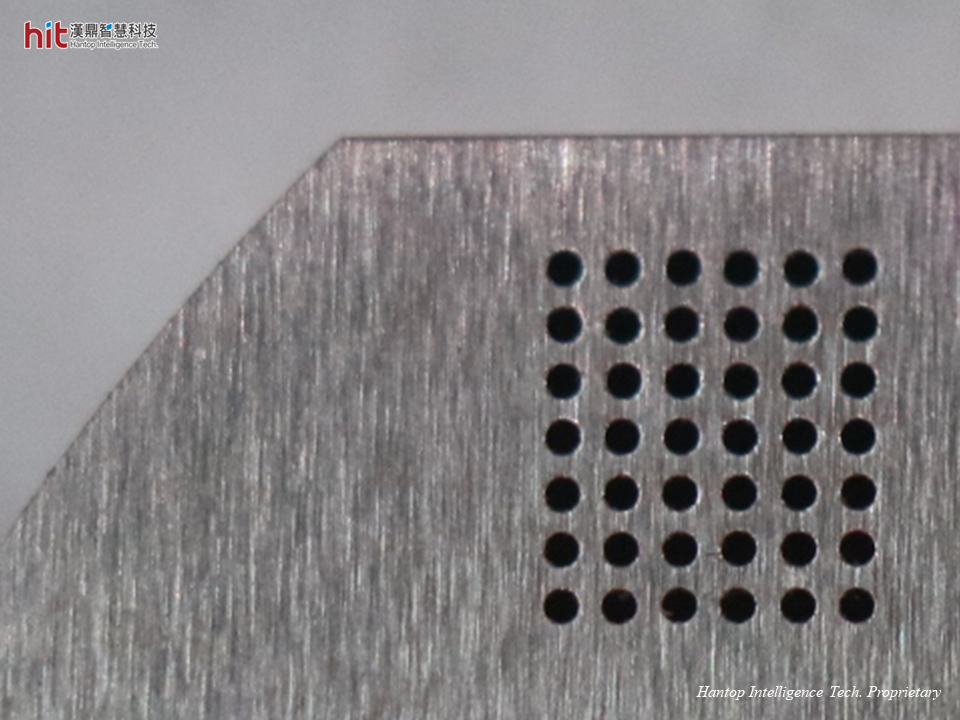
(Bild 1. HIT HSK-E40 Ultraschallbearbeitungsmodul wurde beim Mikrobohren von Nickellegierung Inconel 718 verwendet)
HITs Ziel beim Mikrobohren von Nickellegierung (Inconel 718)
Das Ziel ist es, eine höhere Bearbeitungseffizienz und eine längere Werkzeuglebensdauer beim Mikrobohren von Nickellegierung (Inconel 718) mit der HIT-Ultraschallunterstützten Bearbeitungstechnologie zu erreichen.
Ergebnisse des Ultraschallunterstützten Mikrobohren von Nickellegierung (Inconel 718)
Mikrobohren von Nickellegierung (Inconel 718): Bearbeitungseffizienz
- Die Lösung für das Mikrobohren von Nickellegierung (Inconel 718) in der konventionellen CNC-Bearbeitung bestand darin, die Vorschubgeschwindigkeit zu verringern (ursprüngliche Vorschubgeschwindigkeit: 320 mm/min) und die Schnittgeschwindigkeit zu erhöhen. Allerdings wäre das kontinuierliche Schneiden bei solch hoher Temperatur mit verringerter Vorschubgeschwindigkeit zeitaufwändig und ineffizient; die Erhöhung der Schnittgeschwindigkeit würde zu übermäßiger Schnittwärme und hohen Schnittkräften (verfestigte Schicht) führen, was zu starkem Werkzeugverschleiß führte.
- Einführung des HIT-Ultraschallunterstützten Bearbeitungsprozesses: Der Bearbeitungsmechanismus von HIT-Ultraschall - die hochfrequente Mikrovibration ermöglichte einen leichteren Zufluss des Schneidöls - brachte eine bessere Kühlwirkung und eine bessere Abfuhr der Schneidspäne. Dies half, die Schnittkräfte zu reduzieren.
- Infolgedessen kann mit HIT-Ultraschall die Vorschubgeschwindigkeit auf das Doppelte erhöht werden (optimierte Vorschubgeschwindigkeit: 640 mm/min), während die Schnittgeschwindigkeit niedrig gehalten wird. Dies könnte nicht nur die Schnittwärme reduzieren, sondern auch die verfestigte Schicht auf dem Material vermeiden. Dies führte zu einer 2-mal höheren Bearbeitungseffizienz und einer viel längeren Werkzeuglebensdauer.
Mikrobohren von Nickellegierung (Inconel 718): Werkzeug Lebensdauer
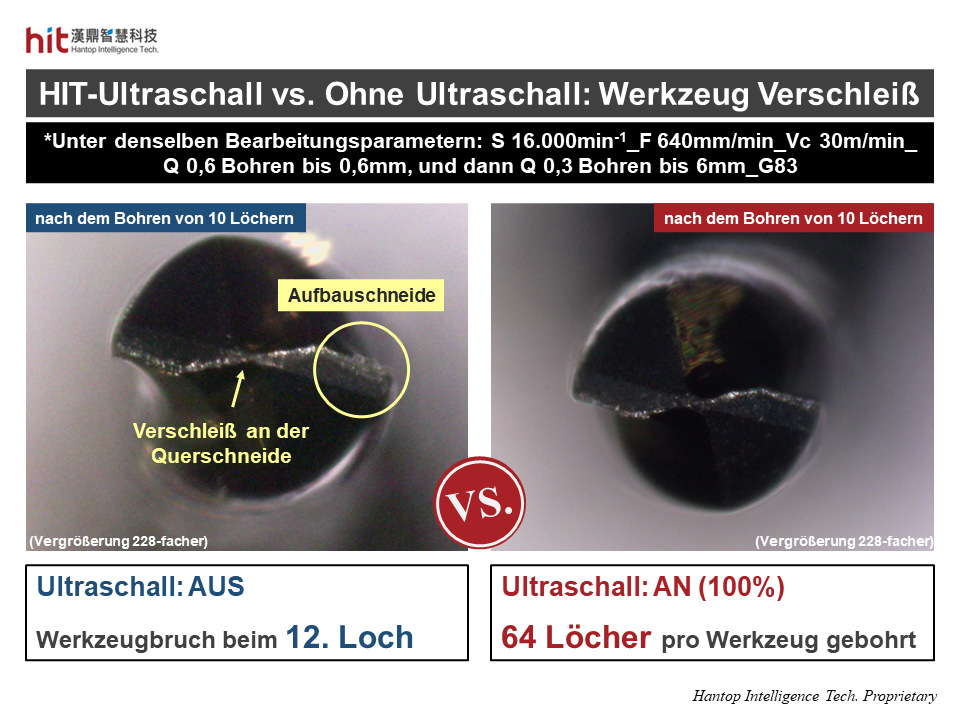
(Bild 2. HIT-Ultraschallunterstütztes Mikrobohren von Nickellegierung Inconel 718, die Verringerung der Schnittwärme und der Schnittkräfte ermöglichte das Bohren von 64 Löchern pro Werkzeug, während ohne Ultraschall das Werkzeug beim 12. Loch brach)

(Bild 3. HIT-Ultraschallunterstütztes Mikrobohren von Nickellegierung Inconel 718 erreichte eine 5-mal längere Werkzeuglebensdauer)
Errungenschaften der HIT-Ultraschall Bearbeitungs Technologie
🕜 Bearbeitungseffizienz - 2-mal höher
⚙️ Werkzeug Lebensdauer - 5-mal länger