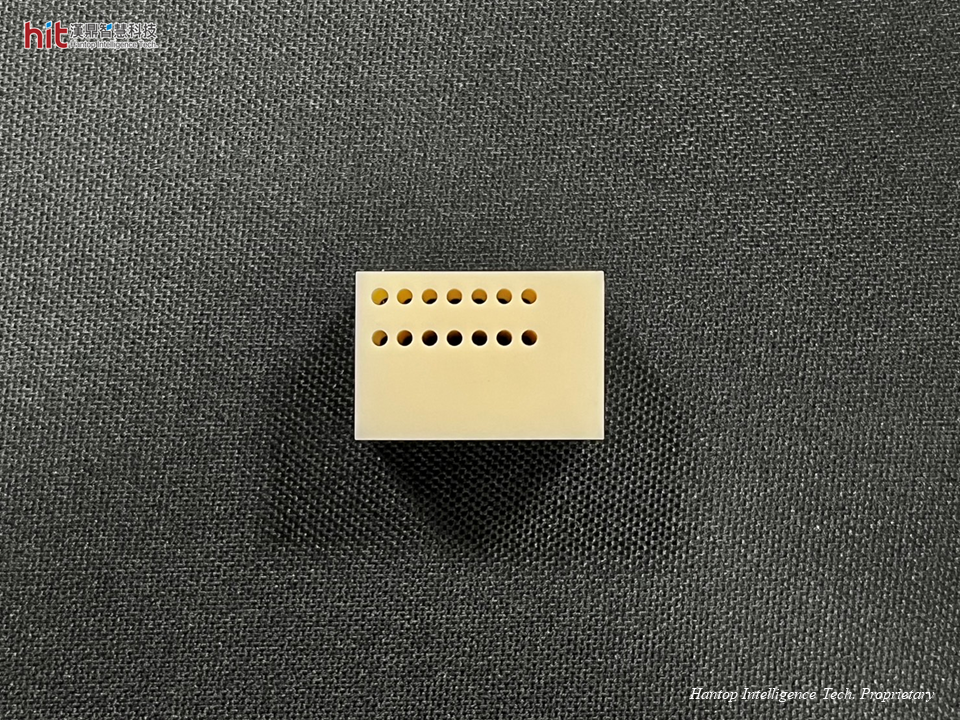
(Figure 1. HIT ultrasonic-assisted machining on deep hole drilling of aluminum oxide ceramic workpiece)
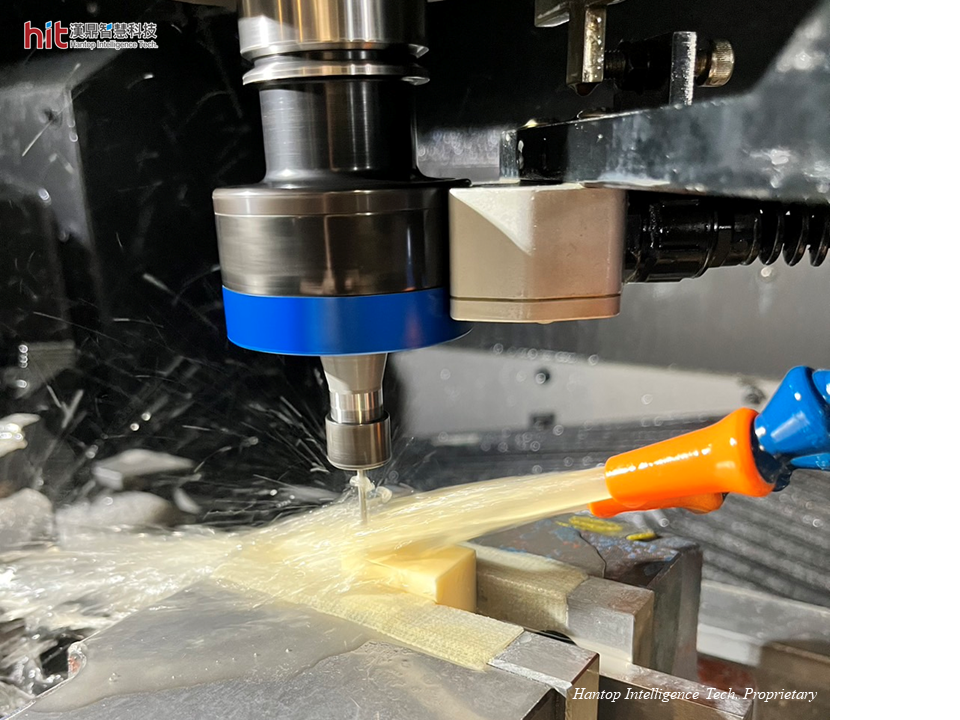
(Figure 2. HSK-E40 ultrasonic toolholder was used on aluminum oxide ceramic deep hole drilling)
HIT's Goal in Machining Aluminum Oxide (Al2O3) Ceramic
The goal is to see the HIT ultrasonic-assisted machining benefits on the deep hole drilling (with very small hole pitch - 0.2mm) of aluminum oxide.
Ultrasonic-Assisted Machining Aluminum Oxide (Al2O3) Ceramic Results
Aluminum Oxide (Al2O3) Ceramic Deep Hole Drilling : Machining Efficiency
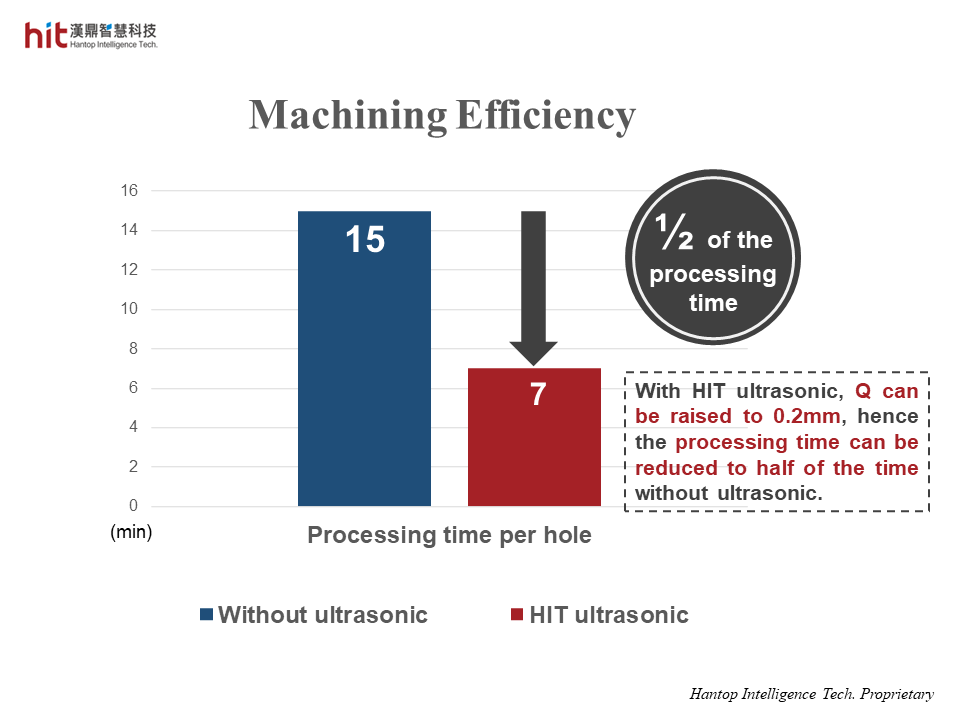
(Figure 3. the processing time was reduced to half of the original with HIT ultrasonic on deep hole drilling of aluminum oxide)
- (Under the same feed rate) With HIT ultrasonic, Q can be raised to 1.5 times higher than the one without ultrasonic (from 0.08mm to 0.2mm).
- The processing time can then be reduced to only half of the time without ultrasonic, with no obvious impact on the hole quality.
Aluminum Oxide (Al2O3) Ceramic Deep Hole Drilling : Hole Quality
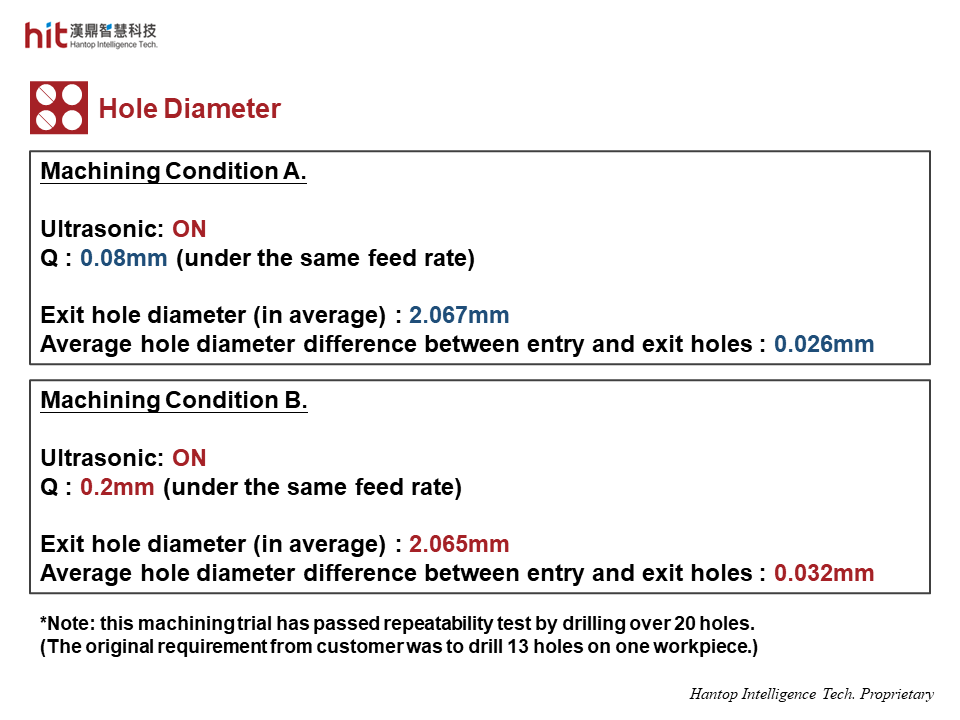
(Figure 4. the hole diameter was well-maintained under higher machining efficiency with HIT ultrasonic-assisted deep hole drilling of aluminum oxide)
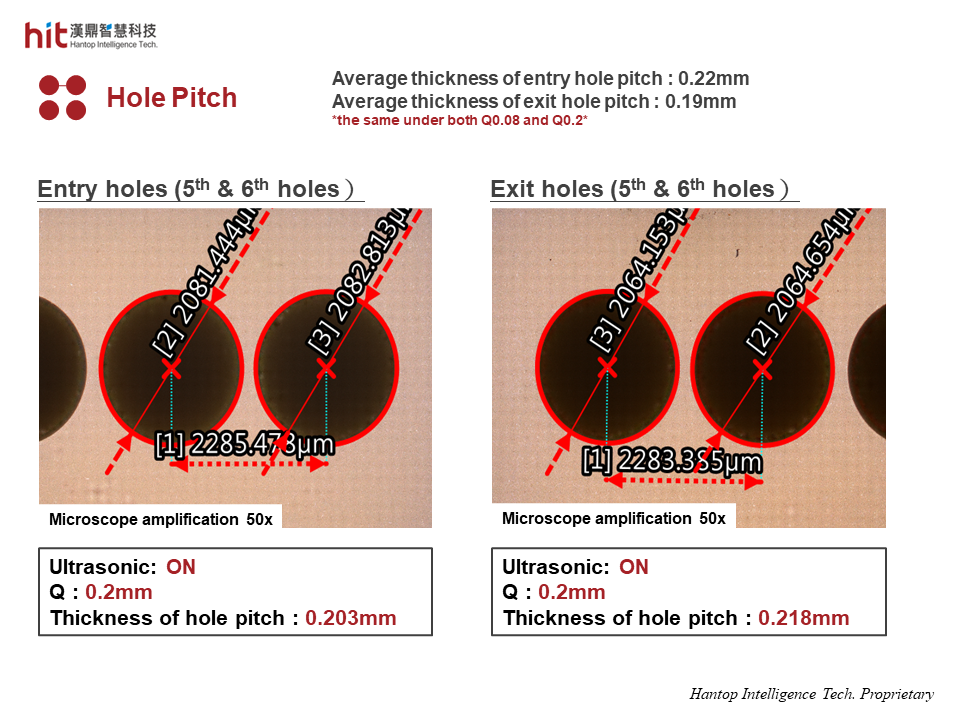
(Figure 5. the hole pitch was well-maintained with no conical holes under higher machining efficiency with HIT ultrasonic-assisted deep hole drilling of aluminum oxide)
- With HIT ultrasonic, the machining efficiency was enhanced (from Q0.08mm to Q0.2mm), and there was no obvious impact on the hole quality.
- With ultrasonic-assisted machining technology, it helped reduce cutting force, which prevented the occurrence of conical holes.
Aluminum Oxide (Al2O3) Ceramic Deep Hole Drilling : Tool Life
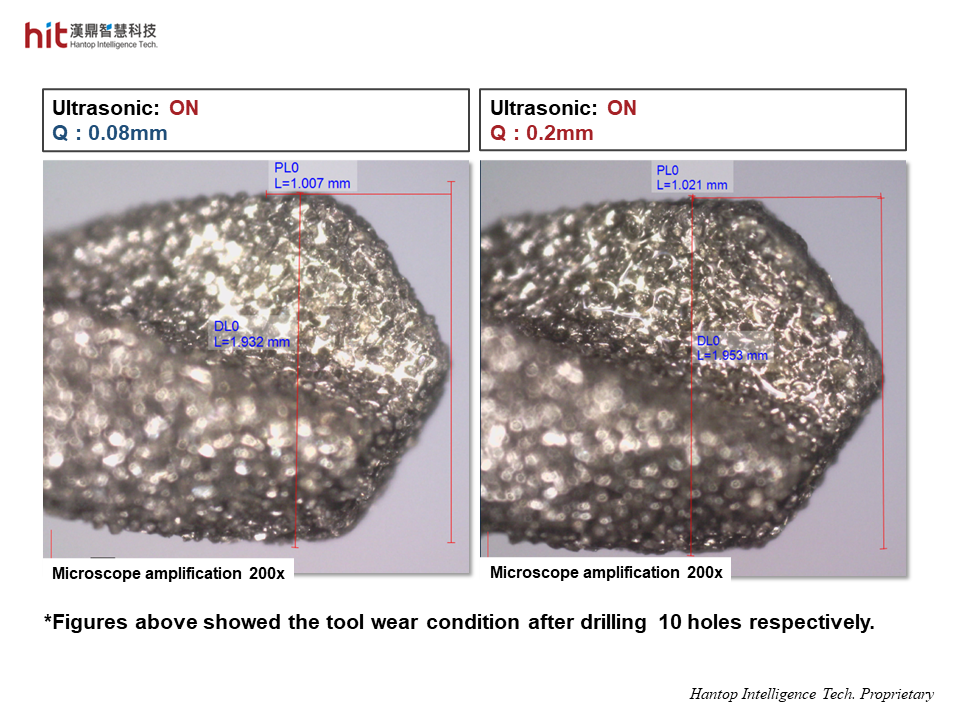
(Figure 6. the comparison of tool wear condition between Q0.08mm and Q0.2mm with HIT ultrasonic-assisted deep hole drilling of aluminum oxide)
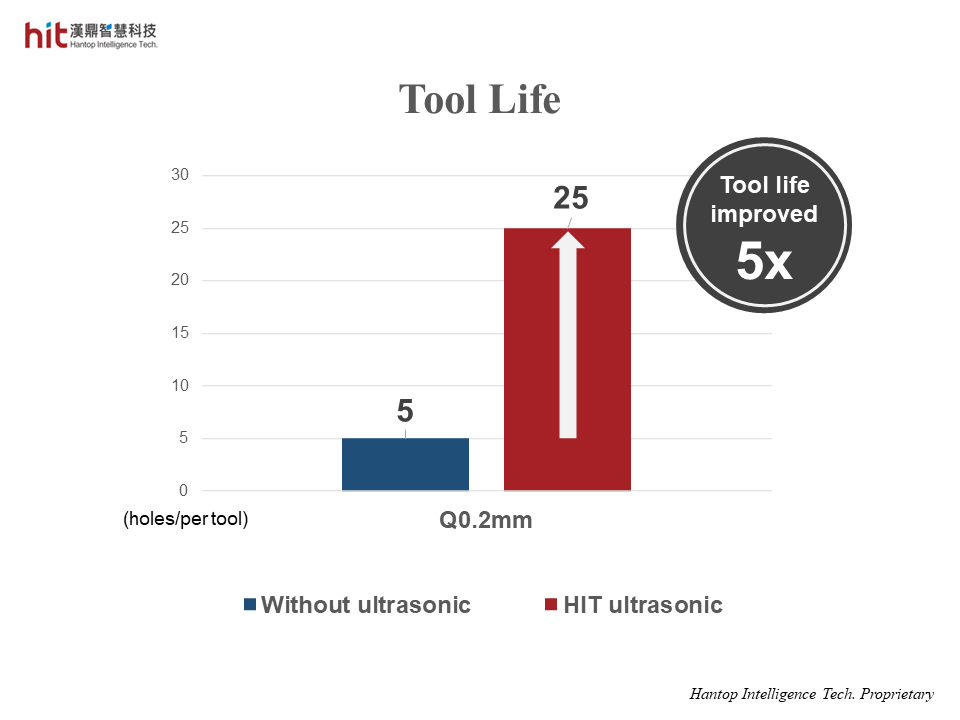
(Figure 7. the tool life was improved 5 times better with HIT ultrasonic on deep hole drilling of aluminum oxide)
- When Q was raised from 0.08mm to 0.2mm, the tool could only drill 5 holes before breakage without ultrasonic.
- With HIT ultrasonic, there was no obvious difference on the tool wear after Q being raised, and the tool could drill up to 25 holes.
HIT Ultrasonic Machining Technology Achievements
🕜 1/2 of the original processing time
📈 Quality - well-maintained
⚙️ Tool Life - improved 5x