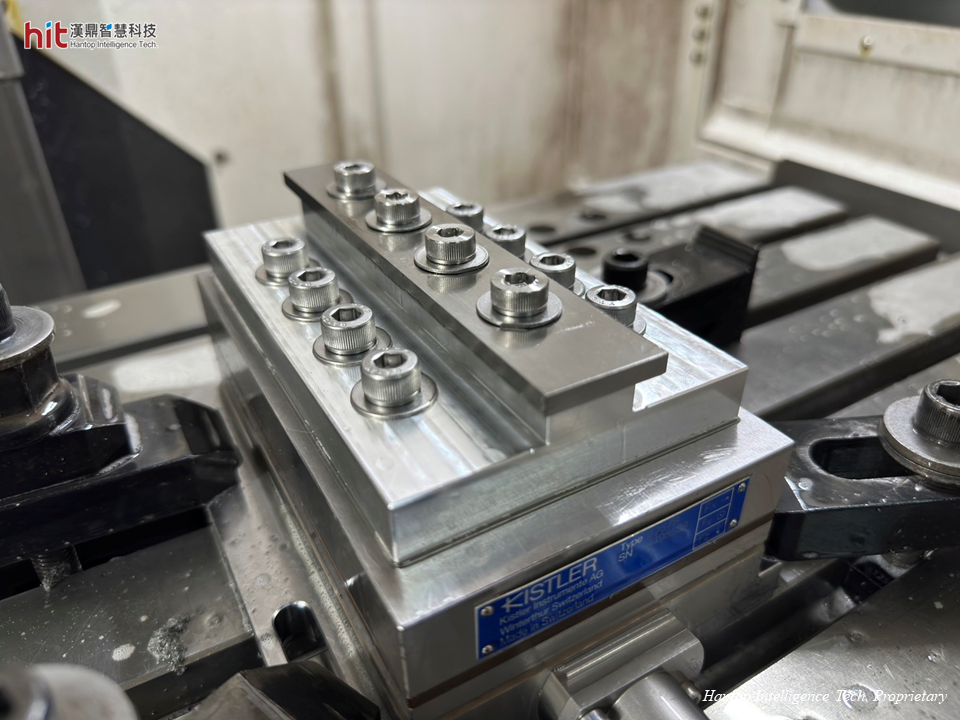
(Figure 1. ultrasonic-assisted side milling on Titanium Alloy workpiece)
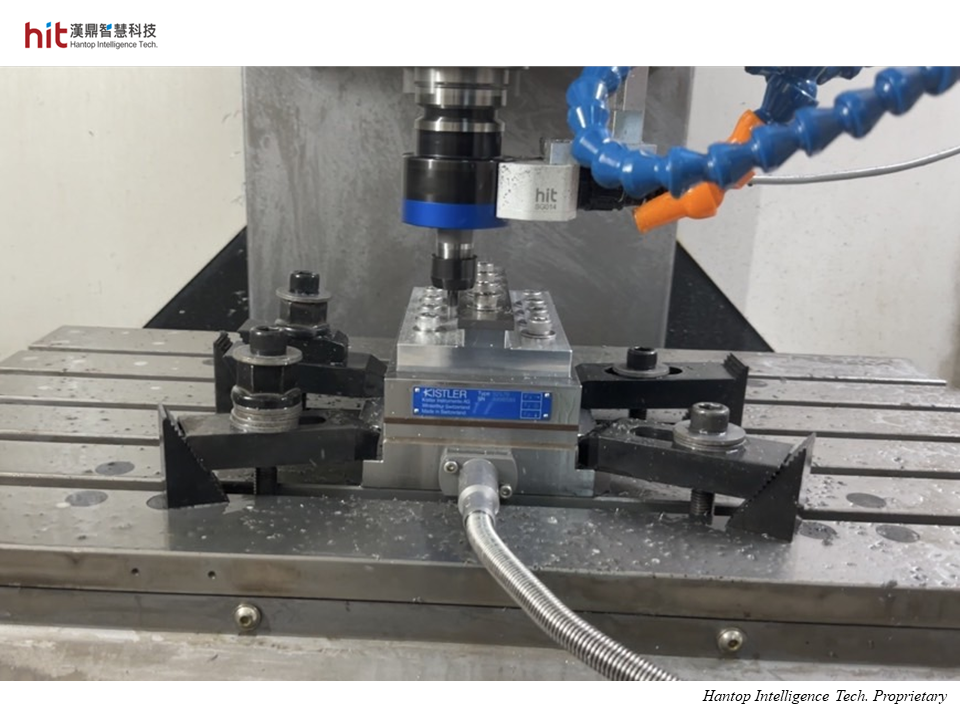
(Figure 2. BT-30 ultrasonic toolholder was used on Titanium Alloy side milling)
HIT's Goal in Machining Titanium Alloy
The goal is to improve tool life under higher machining efficiency, while maintaining high surface quality which meets client's requirement.
Ultrasonic-Assisted Machining Titanium Alloy Results
Titanium Alloy Side Milling : Machining Efficiency
HIT's ultrasonic-assisted machining technology allowed to raise the cutting speed 3 times faster than that without ultrasonic, resulting in the increase in feed rate and machining efficiency.
Titanium Alloy Side Milling : Workpiece Quality
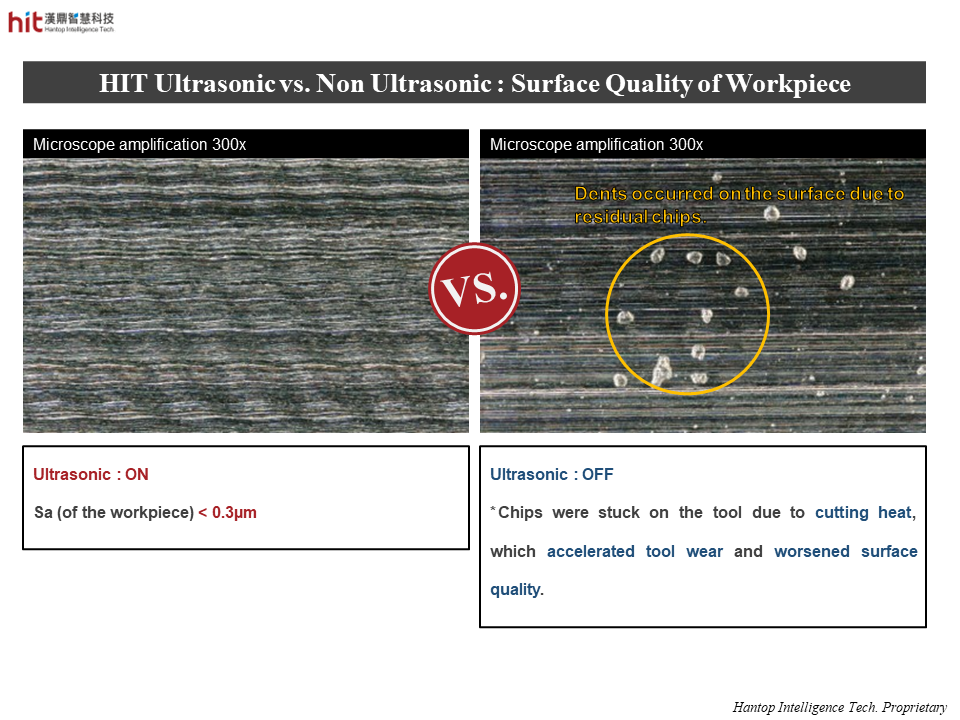
(Figure 3. comparison of titanium alloy side milling workpiece surface quality between HIT ultrasonic and non ultrasonic)
The high-frequency ultrasonic micro-vibration helped reduce the cutting heat, and achieved Sa < 0.3µm, which met with client's requirement on the surface quality.
Titanium Alloy Side Milling : Tool Life
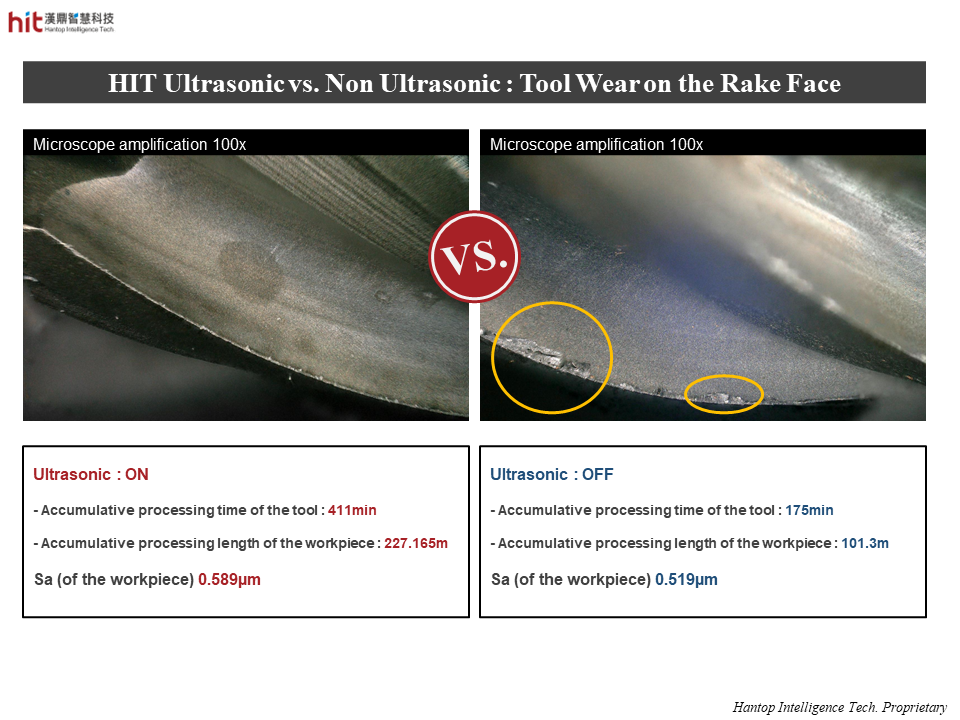
(Figure 4. comparison of tool wear on the rake face between HIT ultrasonic and non ultrasonic machining on titanium alloy side milling)
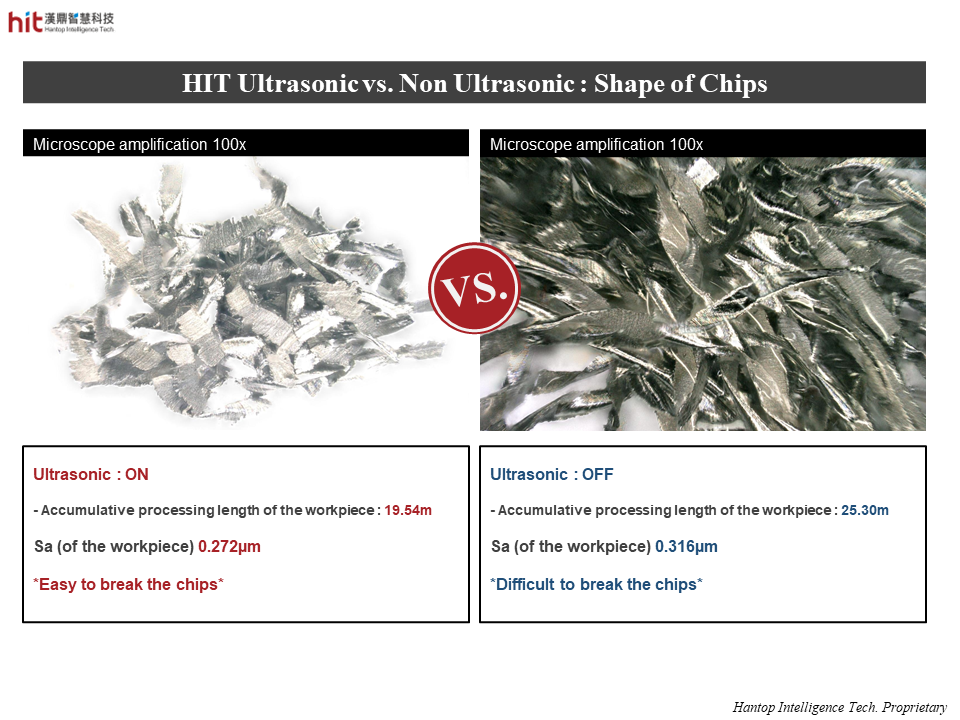
(Figure 5. comparison of shape of chips between HIT ultrasonic and non ultrasonic machining on titanium alloy side milling)
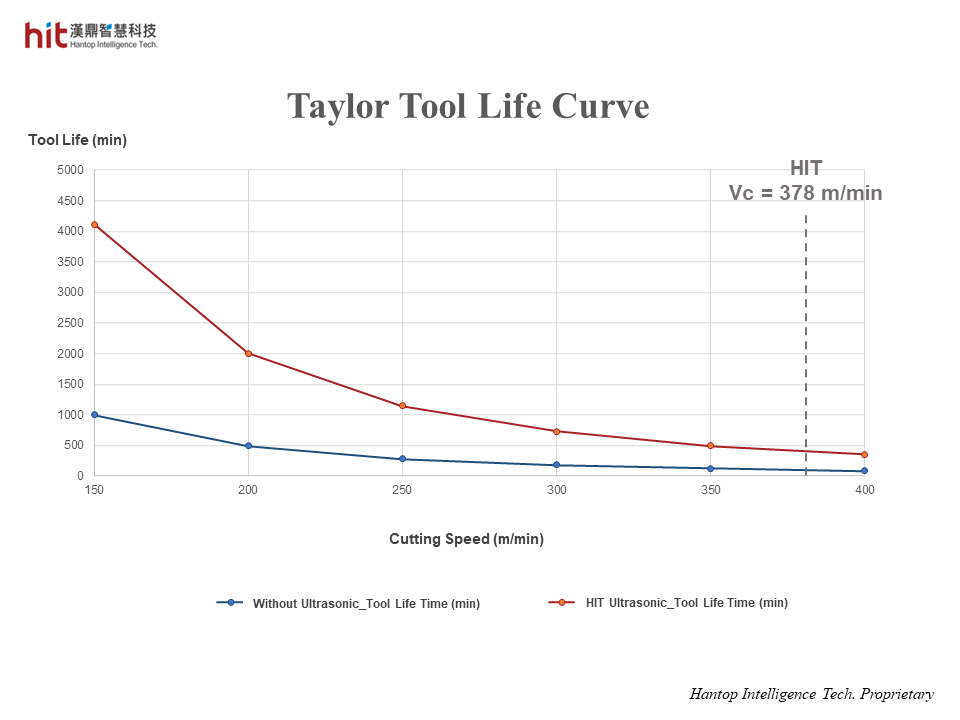
(Figure 6. the Taylor Tool Life Curve shows the potential improved tool life with HIT ultrasonic machining on titanium alloy side milling)
The chips appeared to be larger and very difficult to break in conventional machining. Along with the cutting heat, chips were repeatedly adhesive to tool's rake face, causing breakage on the tool blade.
The high-frequency micro-vibration of HIT's ultrasonic-assisted machining technology helped reduce cutting force and cutting heat, preventing the residual chips from stucking on the tool/workpiece. It also allowed the chips to break easily with no entangled chips.
HIT Ultrasonic Machining Technology Achievements
🕜 Efficiency - 3 times faster than that without ultrasonic
📈 Quality - cutting force/heat reduced, Sa < 0.3µm
⚙️ Tool Life - chips became smaller and easier to break, preventing residual chips from stucking on the tool
💰 With the enhanced machining efficiency and improved tool life, the production capacity can be greatly increased.