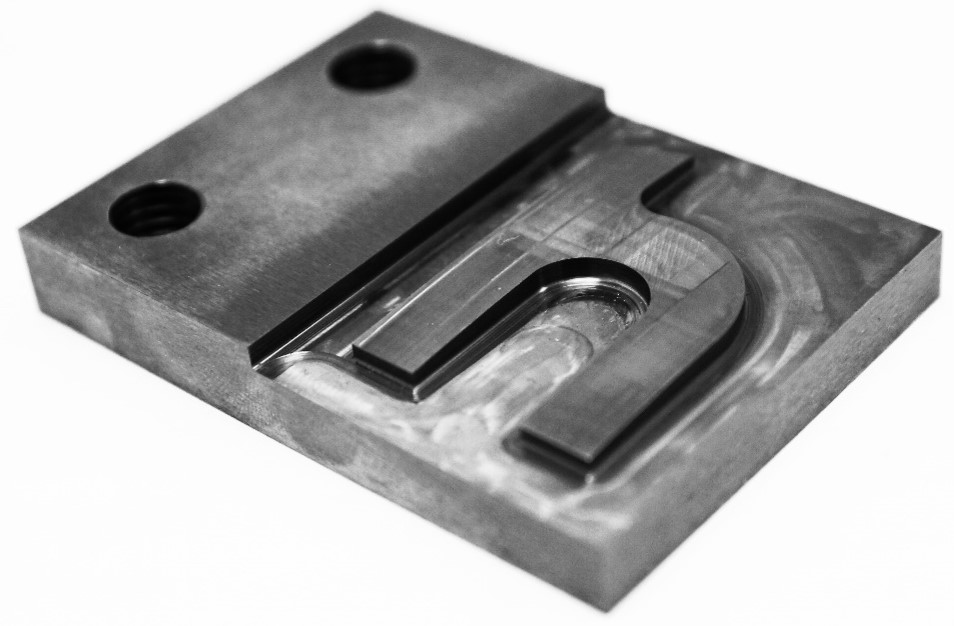
(Figure 1. ultrasonic machining on Tungsten Carbide workpiece)
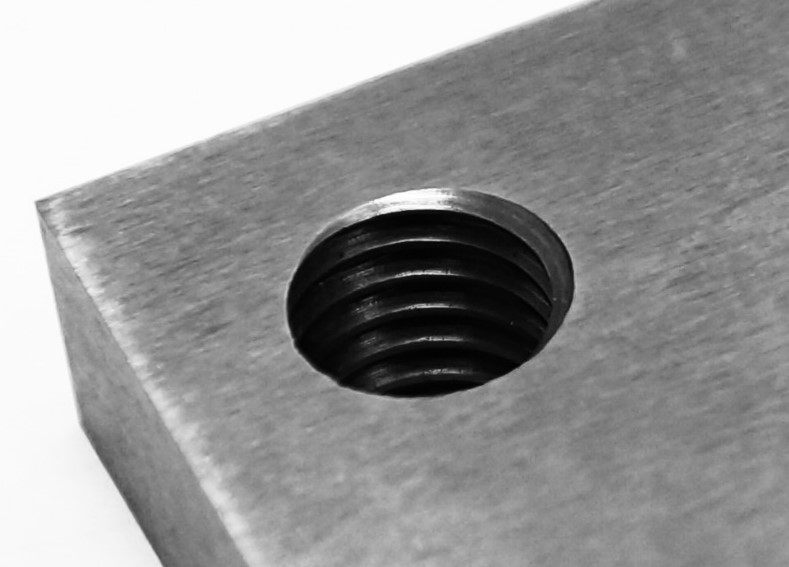
(Figure 2. close-up of ultrasonic threading on Tungsten Carbide workpiece)
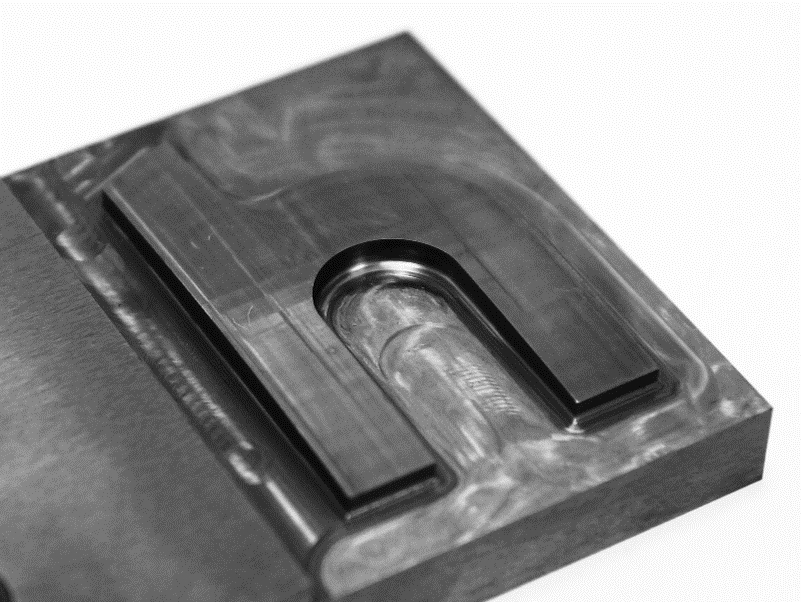
(Figure 3. close-up of ultrasonic h-shape grinding on Tungsten Carbide workpiece)
HIT's Goal in Machining Tungsten Carbide
To compare HIT's ultrasonic effects with the traditional EDM on threading and grinding on Tungsten Carbide.
Ultrasonic-Assisted Machining Tungsten Carbide Results
The processing time of threading on Tungsten Carbide was around 52 minutes and 34 seconds. (less than 1 hour)
The processing time of h-shape grinding on Tungsten Carbide was around 3 hours 37 minutes and 50 seconds. (less than 4 hours)
In the traditional EDM process, the entire process normally took more than 12 hours to complete machining these features on Tungsten Carbide.
With HIT's Ultrasonic Machining Technology, the entire process could be completed within 5 hours.
The surface roughness (Ra) before processing was around 0.936μm.
After processing, the Ra ranged from 0.036 to 0.174μm, with the average of 0.094μm.
HIT Ultrasonic Machining Technology Achievements
🕜 Efficiency - processing time of Threading reduced 83%
- processing time of Grinding reduced 60%
- processing time of the entire process reduced 58%
📈 Quality - (Threading) remained consistent
- (Grinding) surface roughness reduced from Ra > 0.8μm to the average of Ra < 0.1μm
⚙️ Tool Life remained stable
|
HIT ultrasonic |
EDM |
Processing time of threading |
< 60 minutes |
360 minutes |
Processing time of grinding |
< 4 hours |
10 hours |
Processing time (entire process) |
< 5 hours |
> 12 hours |
Surface roughness (Ra) |
(average) 0.094μm |
- |