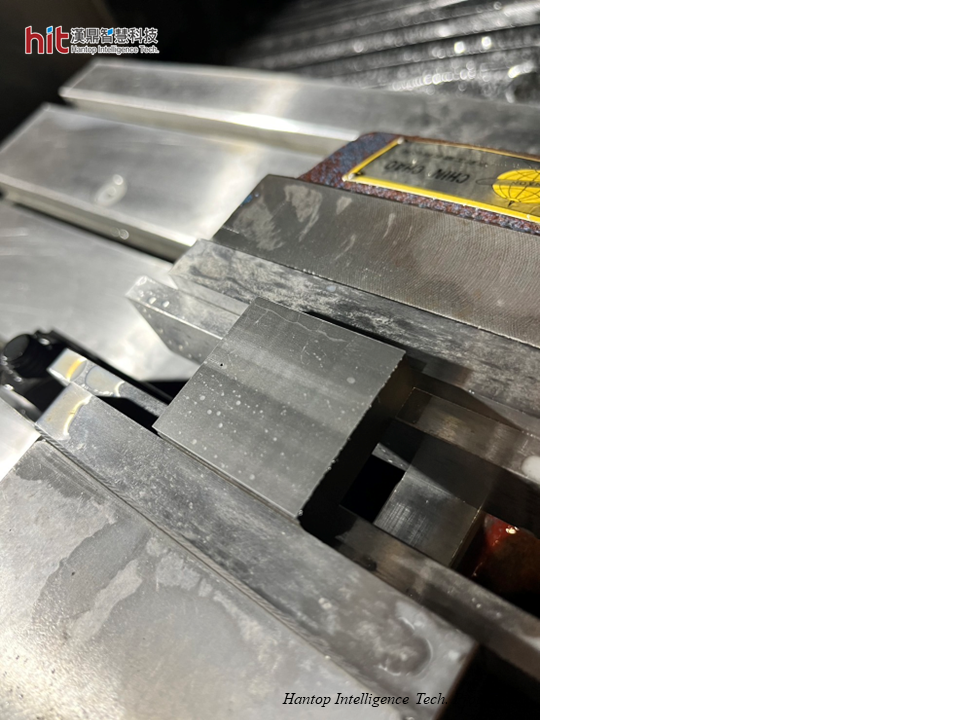
(Figure 1. ultrasonic-assisted bottom milling on AISI-D2 tool steel workpiece)
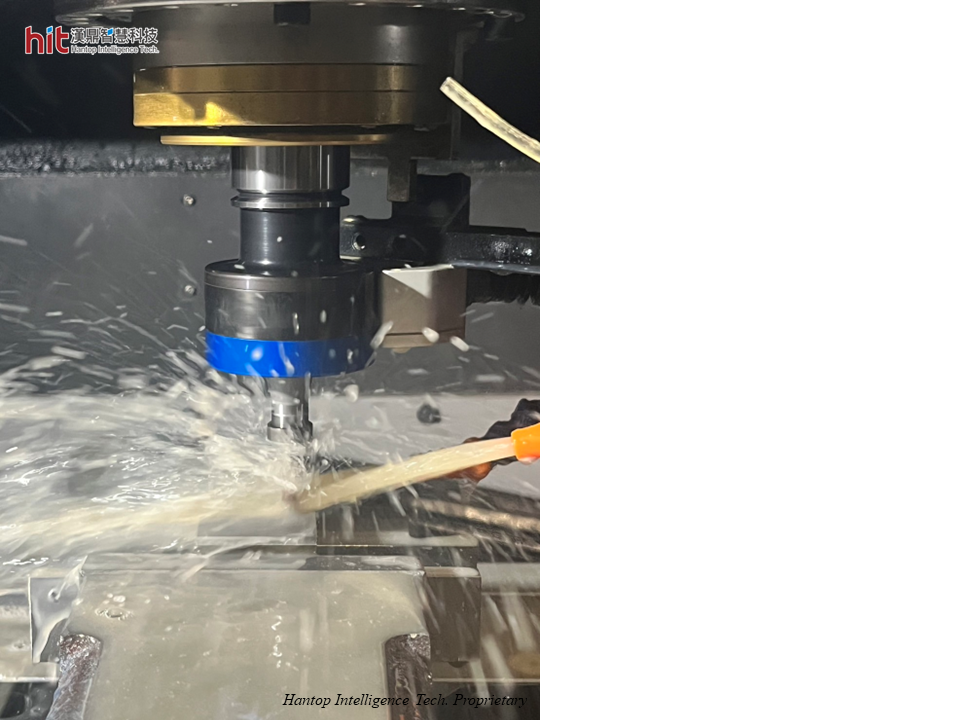
(Figure 2. ultrasonic-assisted bottom milling on AISI-D2 tool steel)
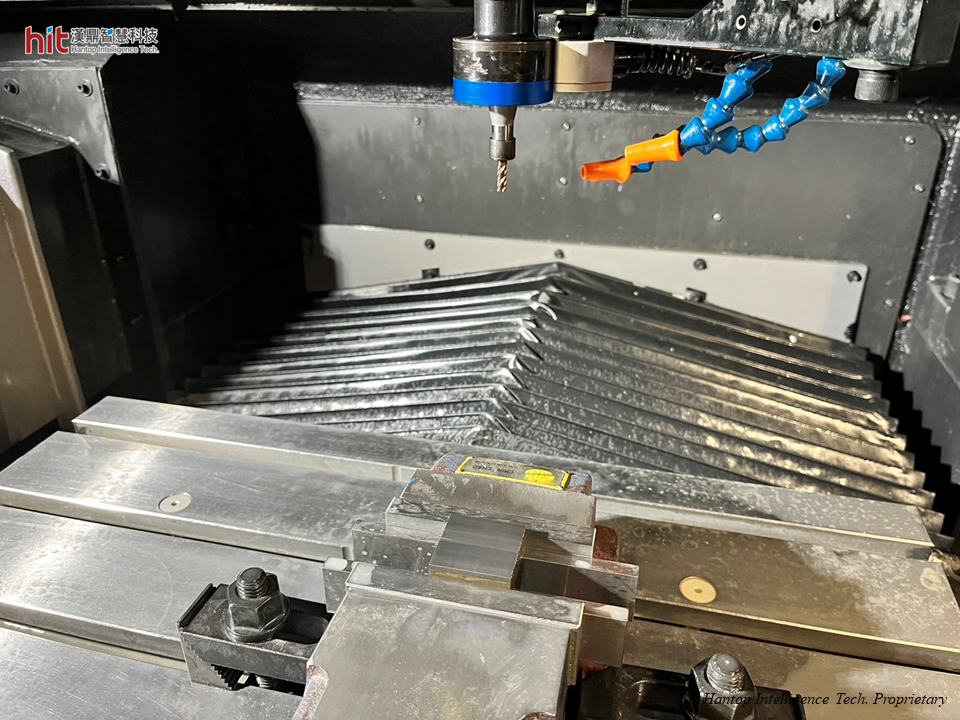
(Figure 3. HSK-E40 ultrasonic toolholder was used on AISI-D2 tool steel bottom milling)
HIT's Goal in Machining AISI-D2 Tool Steel
The goal is to enhance the machining efficiency and improve the stability in tool life, while maintaining great surface quality.
Ultrasonic-Assisted Machining AISI-D2 Tool Steel Results
AISI-D2 Tool Steel Bottom Milling : Machining Efficiency
With HIT Ultrasonic, the cutting speed can be raised 2 times faster than that without ultrasonic, resulting in the increase in feed rate. Consequently, it only took half of the original processing time to complete the bottom milling of AISI-D2 tool steel.
AISI-D2 Tool Steel Bottom Milling : Workpiece Quality
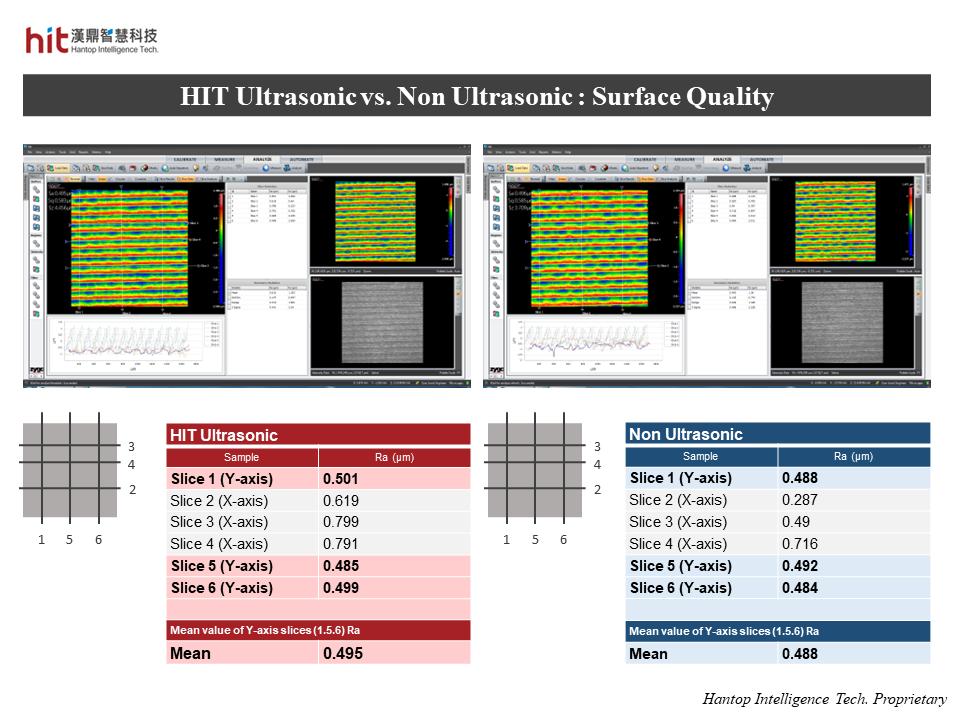
(Figure 4. comparison of bottom milling AISI-D2 tool steel workpiece surface quality between HIT ultrasonic and non ultrasonic)
Throughout the machining trials, HIT discovered that there was no direct influence of ultrasonic-assisted machining technology on the workpiece surface quality.
The key to better surface quality lies in the reduction of the size of processing path pitch. When the size of processing path pitch was reduced, it indicated that the tool needed to run more processing paths to finish the entire process, which took even more processing time.
This is where HIT ultrasonic-assisted machining technology came for help! The biggest benefit of HIT ultrasonic is to enhance the machining efficiency, so that even when the size of processing path pitch was reduced, the processing time would not have to take too long.
AISI-D2 Tool Steel Bottom Milling : Tool Life
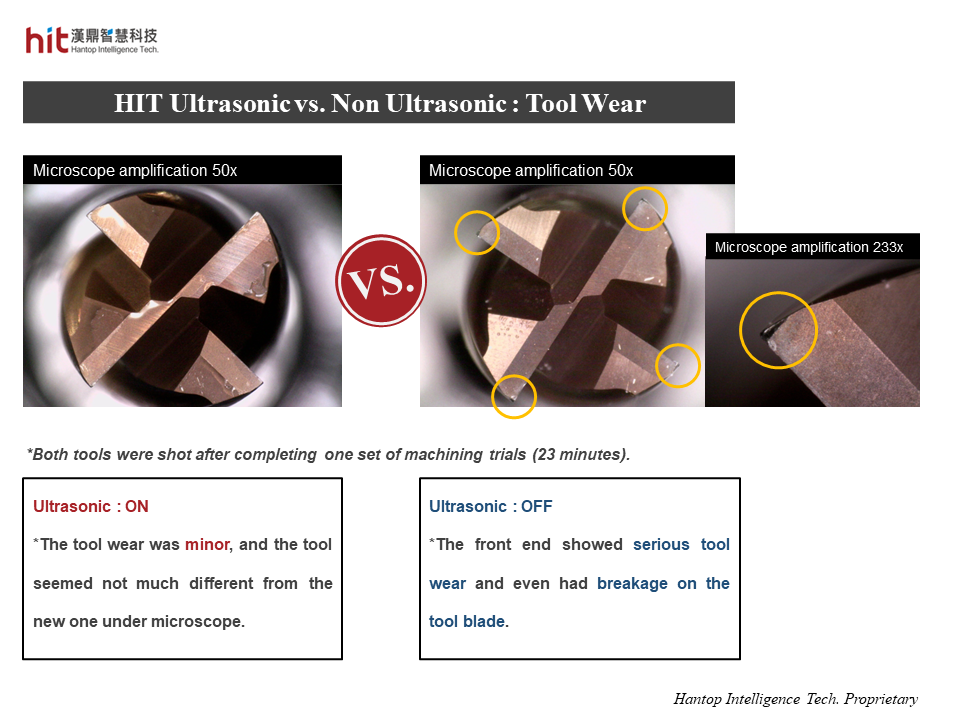
(Figure 5. comparison of the tool wear between HIT ultrasonic and non ultrasonic bottom milling on AISI-D2 tool steel)
With the high-frequency micro-vibration of HIT ultrasonic, the reduction in cutting force helped reduce the tool wear when machining this kind of hard metal steel material.
HIT Ultrasonic Machining Technology Achievements
🕜 Efficiency - 2 times faster than that without ultrasonic
📈 Quality - well-maintained
⚙️ Tool Life - tool wear greatly reduced due to the reduction of cutting force