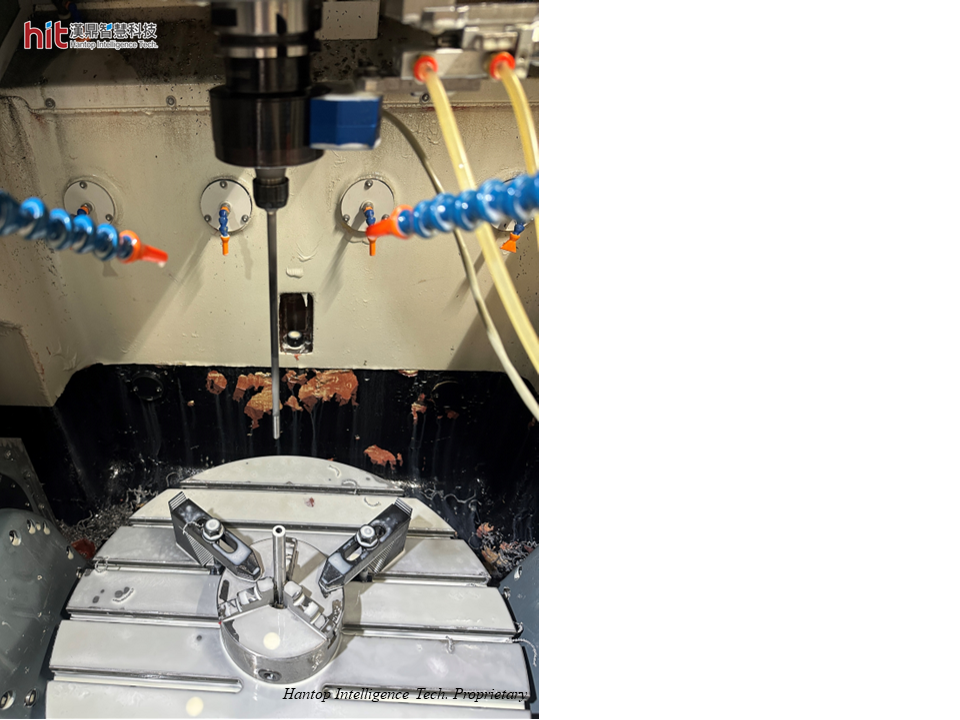
(Figure 1. HSK-A63 ultrasonic toolholder was used on AISI-1045 carbon steel deep hole drilling with gun drill)
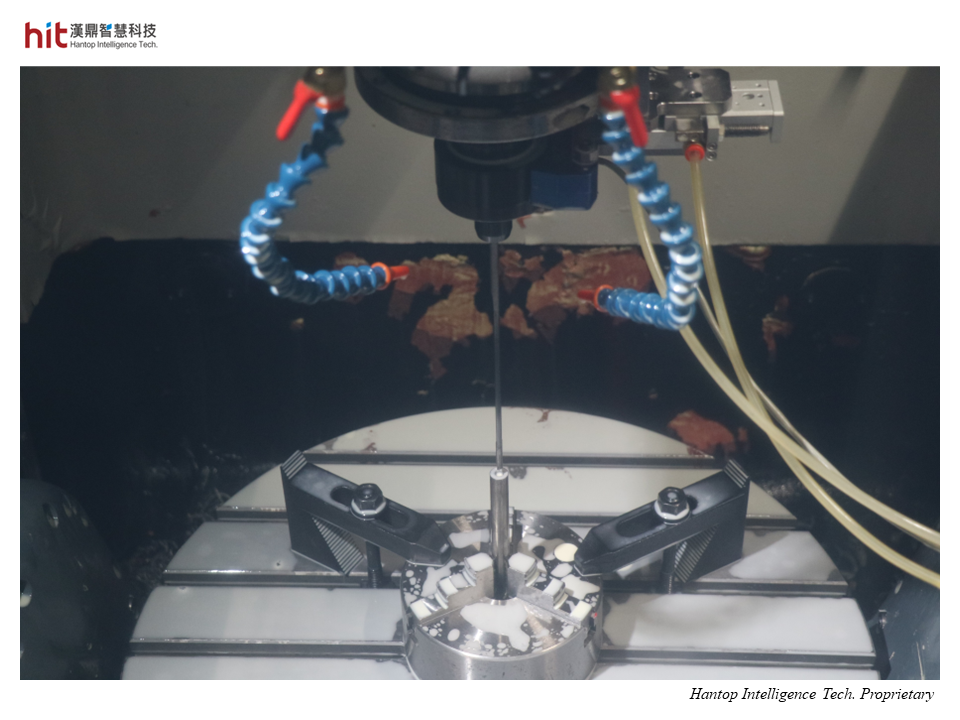
(Figure 2. AISI-1045 carbon steel workpiece and HSK-A63 ultrasonic toolholder during the deep hole drilling process)
HIT's Goal in Machining AISI-1045 Carbon Steel
The goal is to enhance the machining efficiency and see the improvement in the stability of tool life, while maintaining acceptable workpiece quality.
Ultrasonic-Assisted Machining AISI-1045 Carbon Steel Results
AISI-1045 Carbon Steel Deep Hole Drilling with Gun Drill : Machining Efficiency
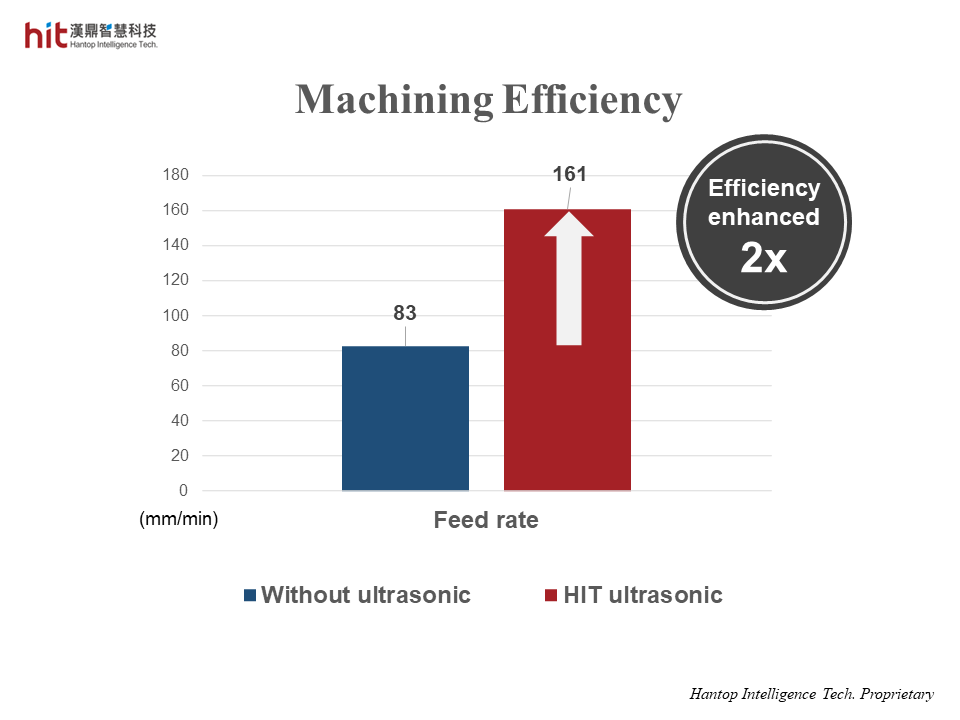
(Figure 3. the machining efficiency was enhanced 2 times higher with HIT Ultrasonic on deep hole drilling of AISI-1045 carbon steel)
- With HIT Ultrasonic, the feed rate can be enhanced 2 times higher than the one suggested by the tooling supplier (under the same rotation speed of 4,600rpm).
- Feed can also be enhanced 2 times higher than the original one with just 40bar of high-pressured Coolant Through Spindle (CTS).
- The entire machining efficiency was enhanced 2 times higher than that without ultrasonic.
AISI-1045 Carbon Steel Deep Hole Drilling with Gun Drill : Workpiece Quality
- With HIT Ultrasonic, it helps reduce cutting force. The tool contacts with the workpiece intermittently during the machining process, which allows for a great reduction in cutting heat.
- The surface roughness (Ra) of the hole wall was well-maintained after feed rate being enhanced 2 times higher than the one suggested by the tooling supplier.
AISI-1045 Carbon Steel Deep Hole Drilling with Gun Drill : Chip Shape & Chip Size
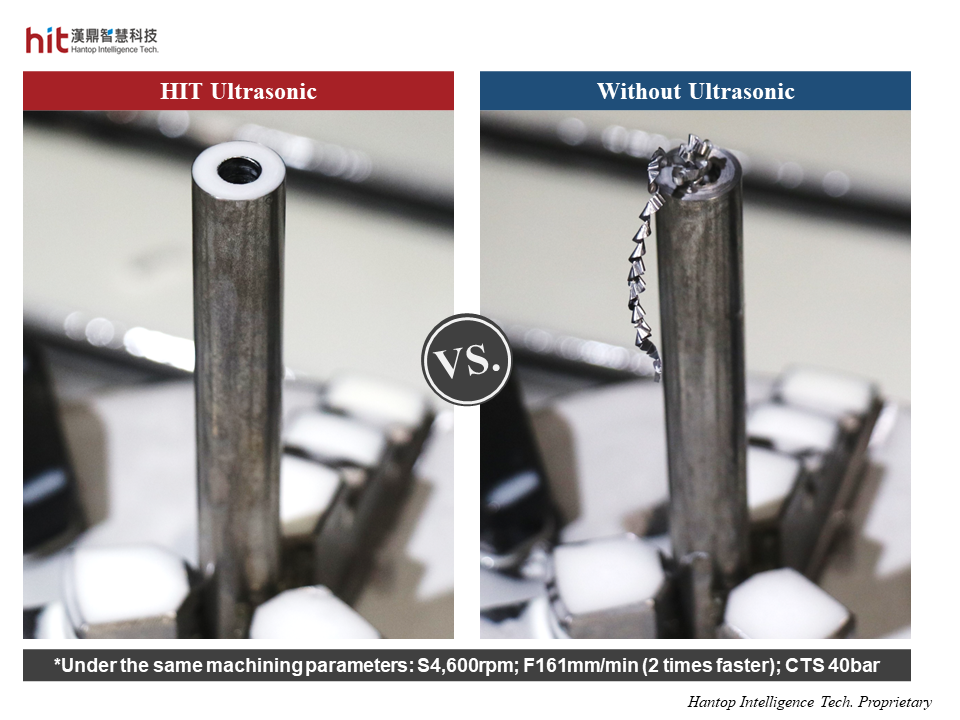
(Figure 4. the comparison of chip removal process between HIT Ultrasonic and Without Ultrasonic on deep hole drilling of AISI-1045 carbon steel workpiece)
- Without ultrasonic, there would be accumulated chips, which were long and hard to remove under 40bar of CTS.
- The feed rate was enhanced 2 times higher with only 40bar of CTS with HIT Ultrasonic. The high-speed micro-vibration helps chips to break naturally once it reached certain volume.
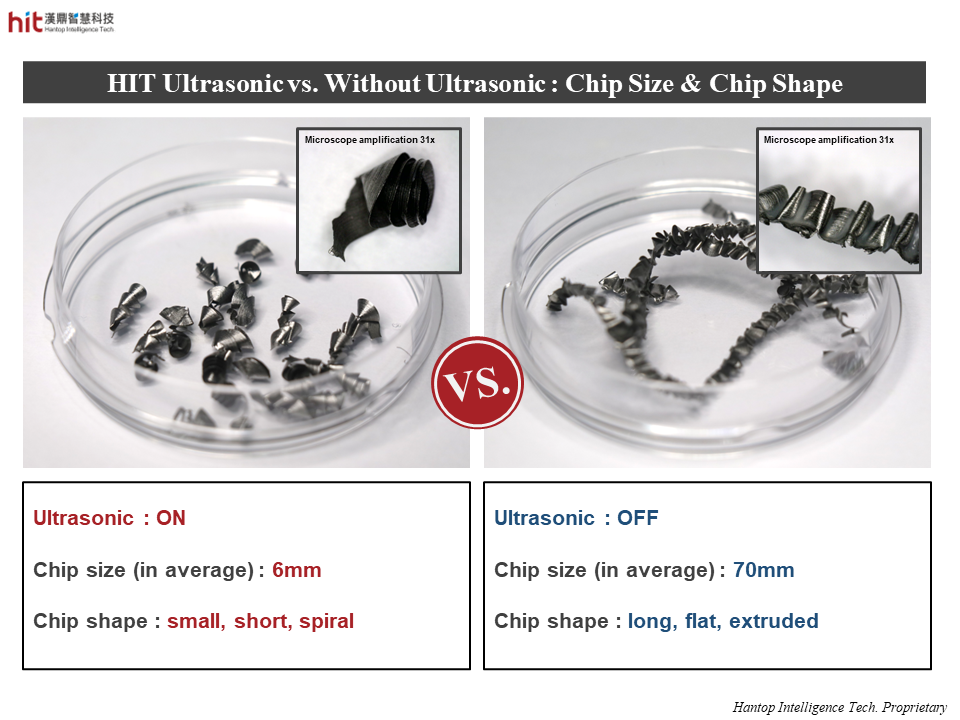
(Figure 5. the comparison of chip size and chip shape between HIT Ultrasonic and Without Ultrasonic on deep hole drilling of AISI-1045 carbon steel)
- The chips became shorter, and the chip size was 91% smaller than that without ultrasonic (from an average of 70mm to 6mm).
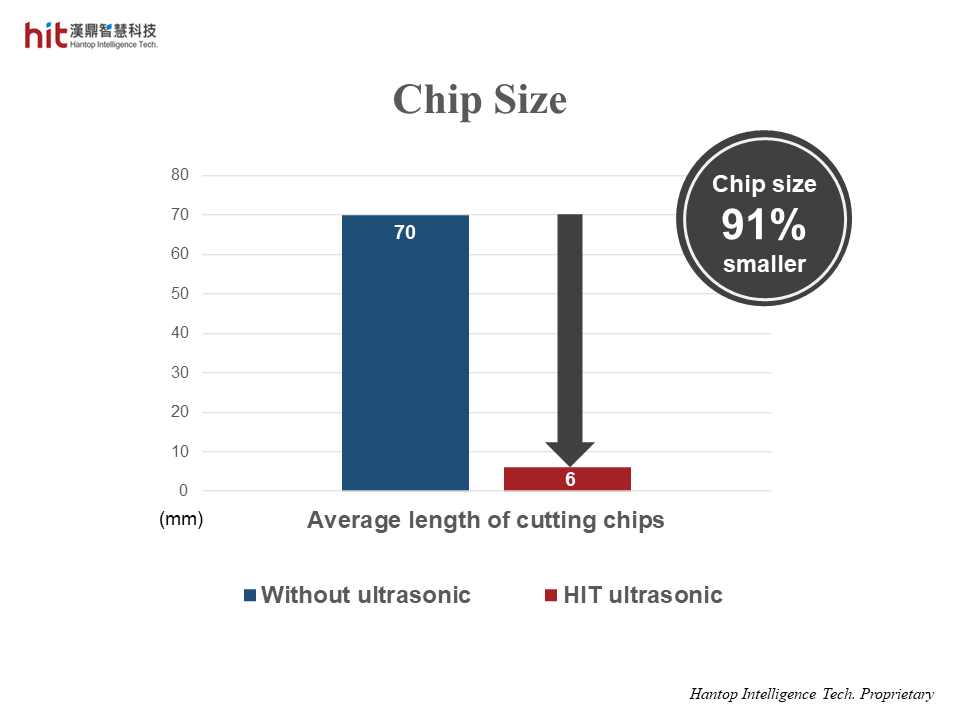
(Figure 6. the chip size was 91% smaller and shorter with HIT Ultrasonic on deep hole drilling of AISI-1045 carbon steel)
HIT Ultrasonic Machining Technology Achievements
🕜 Efficiency - enhanced 2x
📈 Quality - well-maintained
⚙️ Chip Size - 91% smaller and shorter