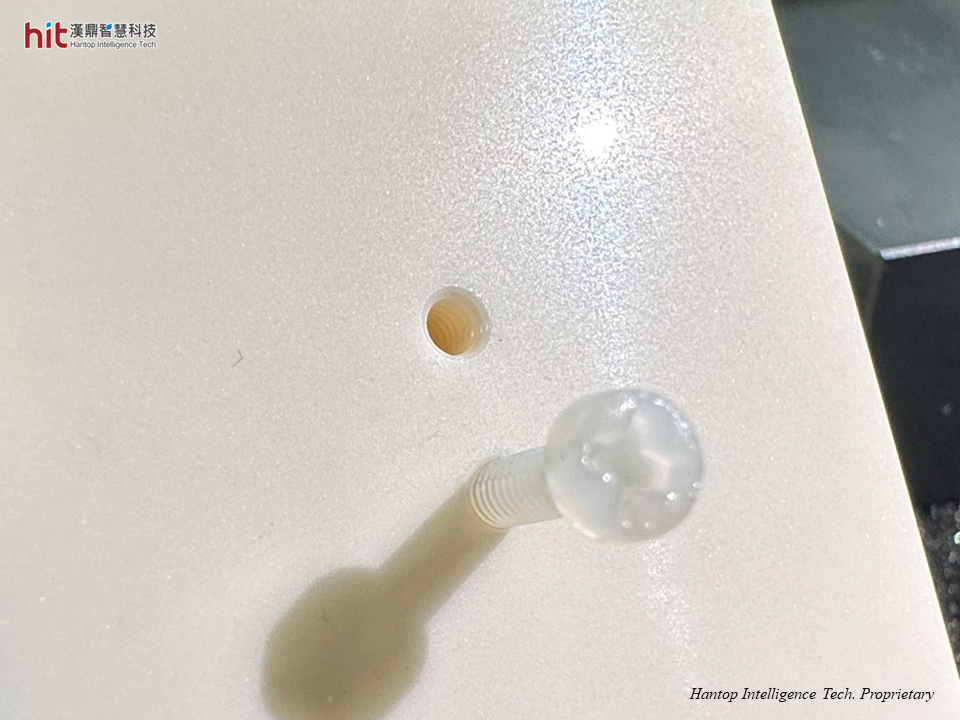
(Figure 1. HSK-E40 ultrasonic machining module was used on the machining of aluminum oxide ceramic M2 internal threading)
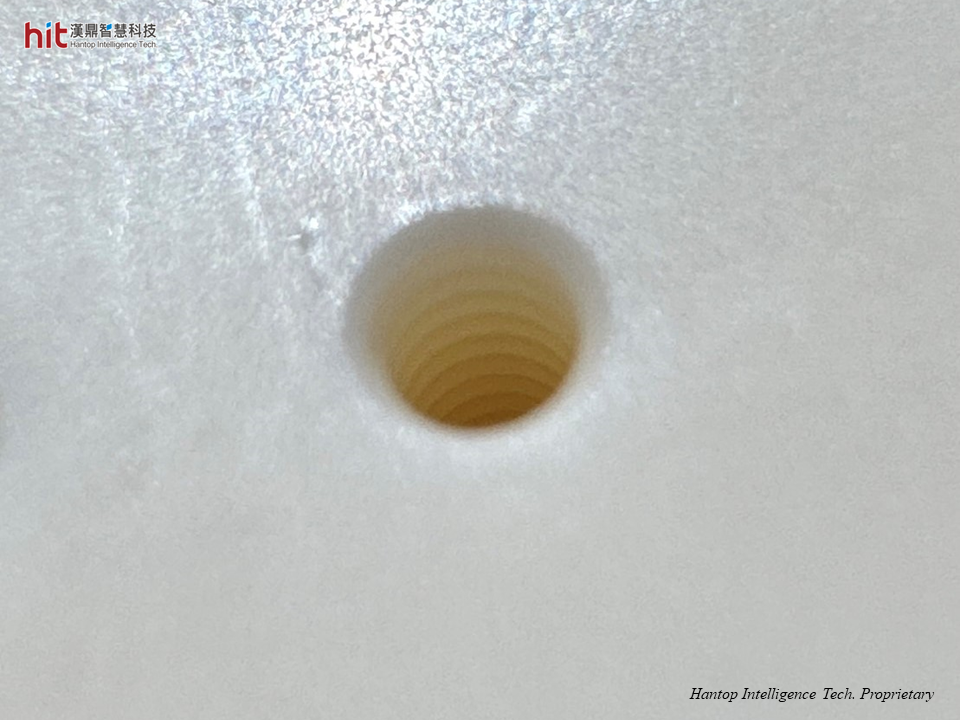
(Figure 2. HIT ultrasonic-assisted machining of aluminum oxide ceramic M2 internal threading workpiece)
HIT's Goal in Machining Aluminum Oxide (Al2O3) Ceramic
The goal is to successfully make an M2 internal thread on aluminum oxide ceramic with HIT ultrasonic-assisted machining technology on CNC machine tool with single type thread mill.
Ultrasonic-Assisted Machining Aluminum Oxide (Al2O3) Ceramic Results
Aluminum Oxide (Al2O3) Ceramic M2 Internal Threading : Machining Efficiency
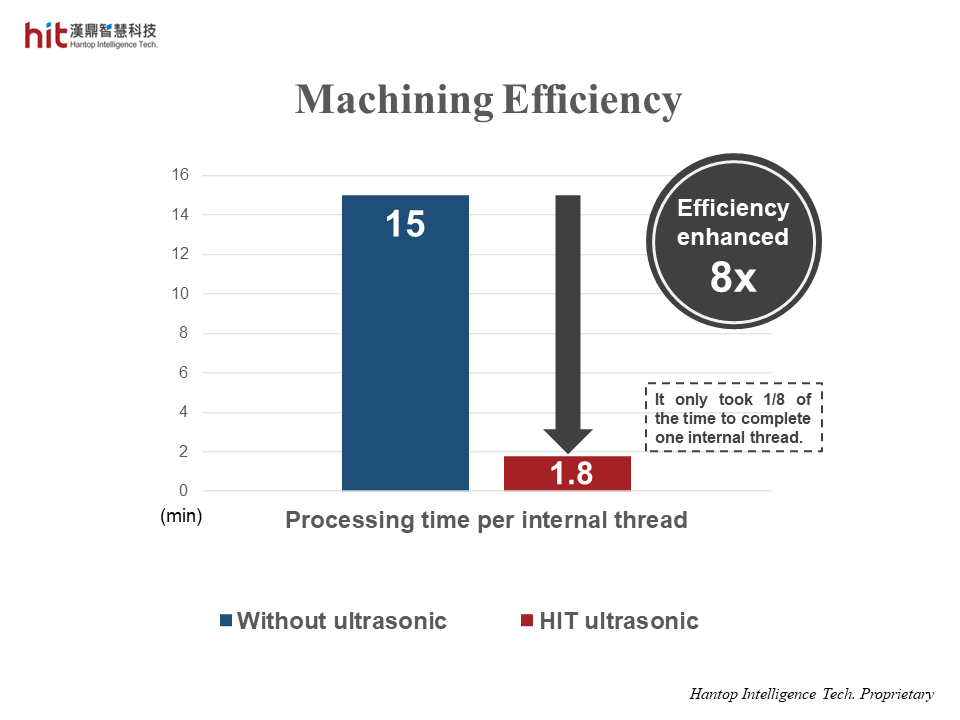
(Figure 3. the machining efficiency was enhanced 8 times higher with HIT Ultrasonic on M2 internal threading of aluminum oxide ceramic)
- (Under the same feed per revolution) With HIT ultrasonic, both rotation speed and feed rate can be enhanced over 3 times higher than the ones suggested by the tooling supplier.
- Firstly, the rotation speed was raised from 10,000 to 30,000rpm, with the feed rate being raised from 20 to 60mm/min.
- After that, HIT discovered that the process could go even faster. The feed per revolution was then being raised, resulting in the feed rate eventually being raised from 20 to 300mm/min (15 times higher than the original).
- The processing time of completing one internal thread was reduced to 1/8 of the processing time without ultrasonic.
- With HIT ultrasonic, it helped reduce the cutting force under high-speed machining, which accomplished the machining of M2 internal thread on aluminum oxide ceramic.
Aluminum Oxide (Al2O3) Ceramic M2 Internal Threading : Workpiece Quality
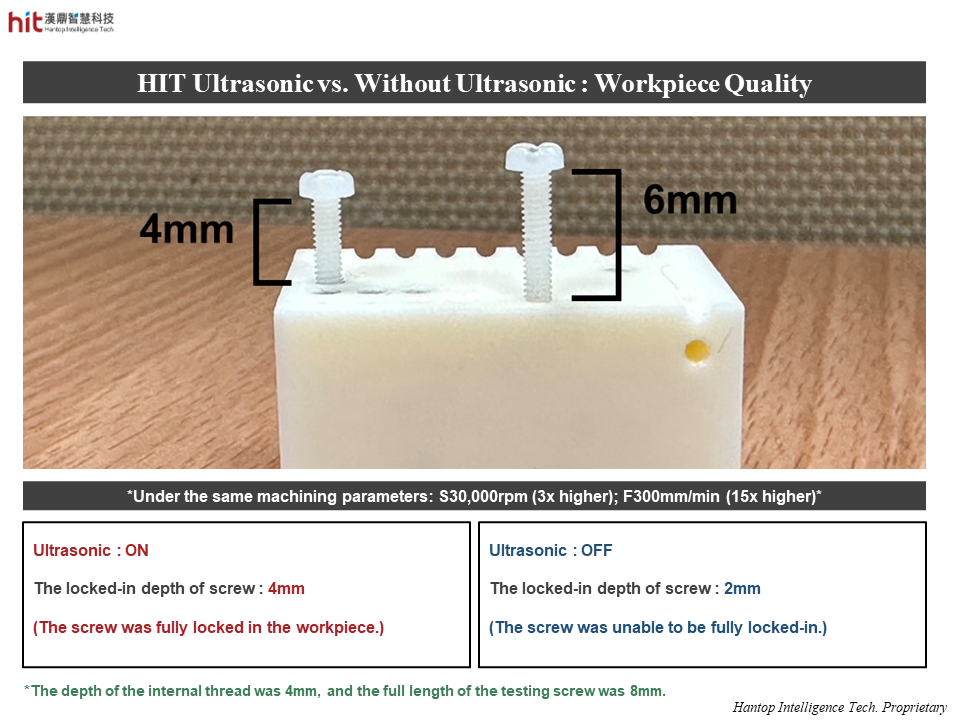
(Figure 4. the comparison of workpiece quality between HIT Ultrasonic and Without Ultrasonic on M2 internal threading of aluminum oxide ceramic)
- With HIT ultrasonic, the high frequency micro-vibration allowed for intermittent contact between the tool and workpiece, which greatly helped reduce cutting heat.
- The reduction in both cutting force and cutting heat under high-speed (rotation speed 3x higher, and feed rate 15x higher) machining contributed to the completeness of the M2 internal thread profile.
Aluminum Oxide (Al2O3) Ceramic M2 Internal Threading : Tool Life

(Figure 5. the comparison of tool wear between HIT Ultrasonic and Without Ultrasonic on M2 internal threading of aluminum oxide ceramic)
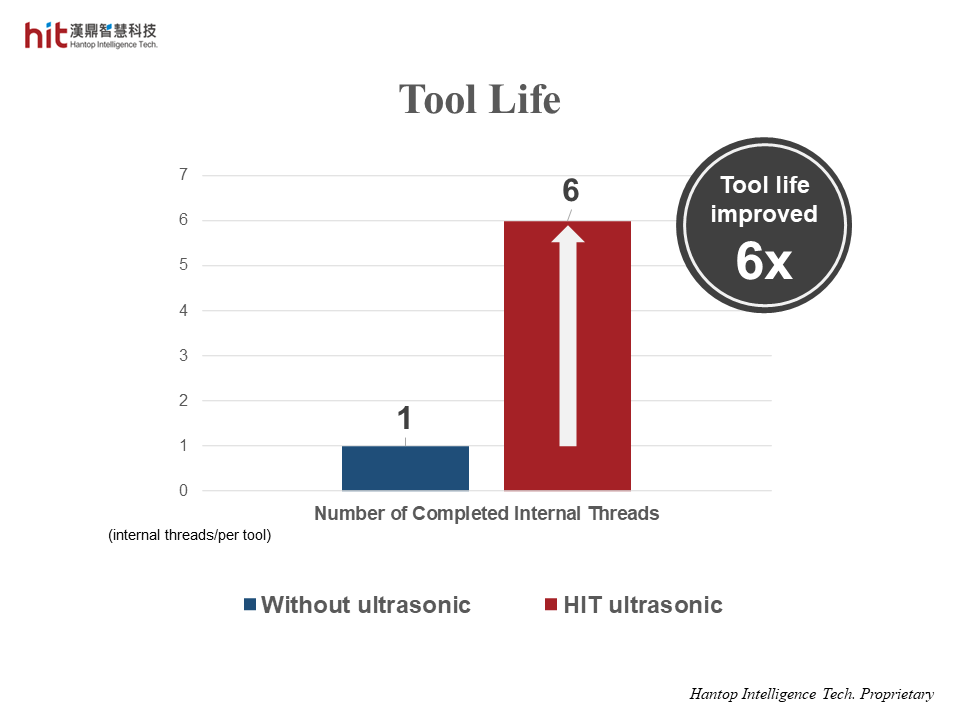
(Figure 6. the tool life was improved 6 times higher with HIT Ultrasonic on M2 internal threading of aluminum oxide ceramic)
- The optimized machining parameters (rotation speed 3x higher, and feed rate 15x higher) were to present the best of ultrasonic-assisted machining technology, and as an accelerated test on the tool life.
- Under the high-speed ultrasonic-assisted machining process, the tool can complete 6 internal threads; whereas the tool could only complete 1 internal thread without ultrasonic (but the test screw was unable to be fully locked into the internal thread).
HIT Ultrasonic Machining Technology Achievements
🕜 Efficiency - enhanced 8x
📈 Quality - complete profile
⚙️ Tool Life - improved 6x