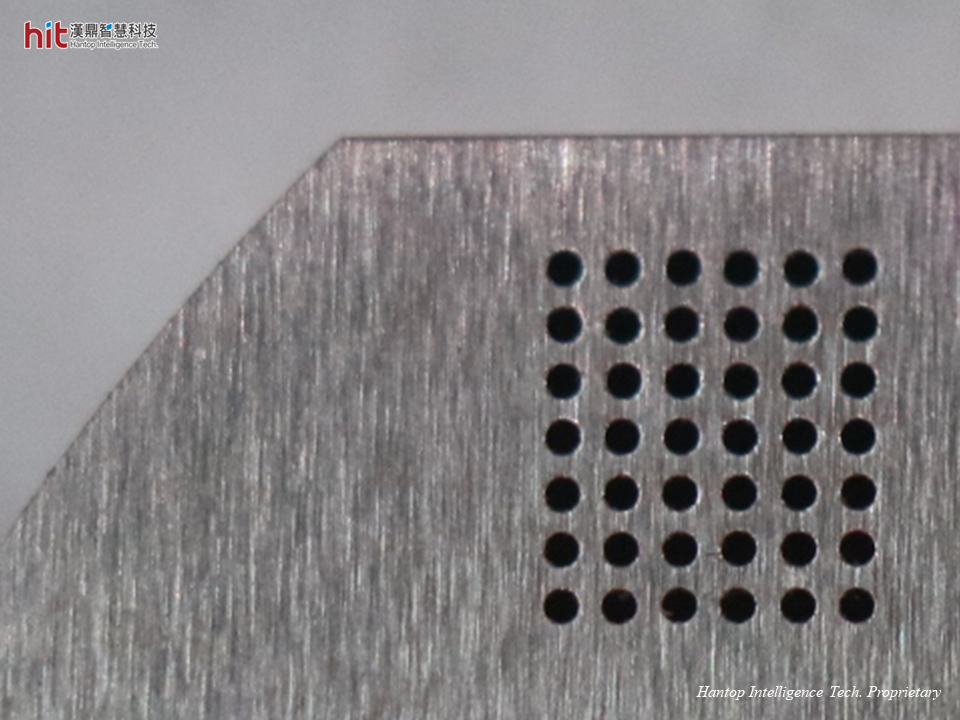
(Figure 1. HIT HSK-E40 ultrasonic machining module was used on Nickel Alloy Inconel 718 micro-drilling)
HIT's Goal in Keyway Side Milling of Nickel Alloy (Inconel 718)
The goal is to achieve higher machining efficiency and longer tool life on micro-drilling of nickel alloy (Inconel 718) with HIT ultrasonic-assisted machining technology.
Ultrasonic-Assisted Keyway Side Milling of Nickel Alloy (Inconel 718) Machining Results
Nickel Alloy (Inconel 718) Keyway Side Milling: Machining Efficiency
- The solution to micro-drilling Nickel Alloy (Inconel 718) in conventional machining was to decrease feed rate (original feed rate: 320mm/min) and increase cutting speed. However, continuous cutting under such high temperature, decreasing feed rate would be time-consuming and inefficient; increasing cutting speed would have excessive cutting heat and high cutting force (work-hardened layer), which led to serious tool wear.
- Introduction of HIT ultrasonic-assisted machining process: the machining mechanism of HIT ultrasonic - the high frequency micro-vibration allowed for easier inflow of cutting fluid - brought better cooling effect and better evacuation of cutting chips. This helped reduce cutting force.
- As a result, with HIT ultrasonic, it can enhance 2x of feed rate (optimized feed rate: 640mm/min) while maintaining low cutting speed. This could not only reduce cutting heat, but also avoid the work-hardened layer on the material. It resulted in 2x higher machining efficiency, and much longer tool life.
Nickel Alloy (Inconel 718) Keyway Side Milling: Tool Life
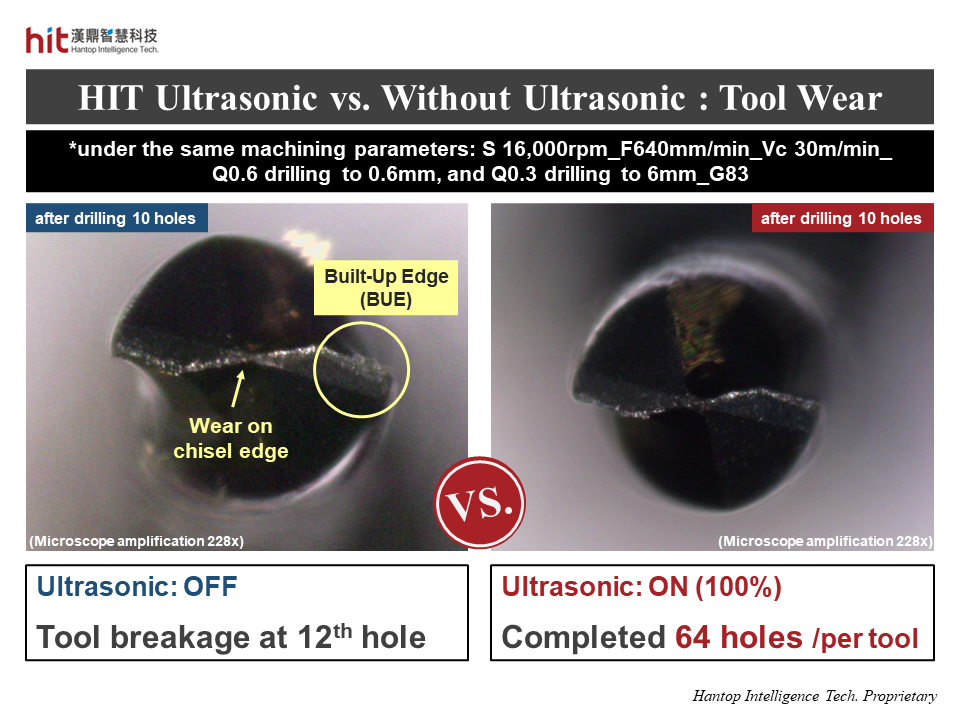
(Figure 2. HIT ultrasonic-assisted micro-drilling of Nickel Alloy Inconel 718, the reduction in cutting heat and cutting force allowed for drilling 64 holes per tool, while the tool breakage happened at 12th hole without ultrasonic)
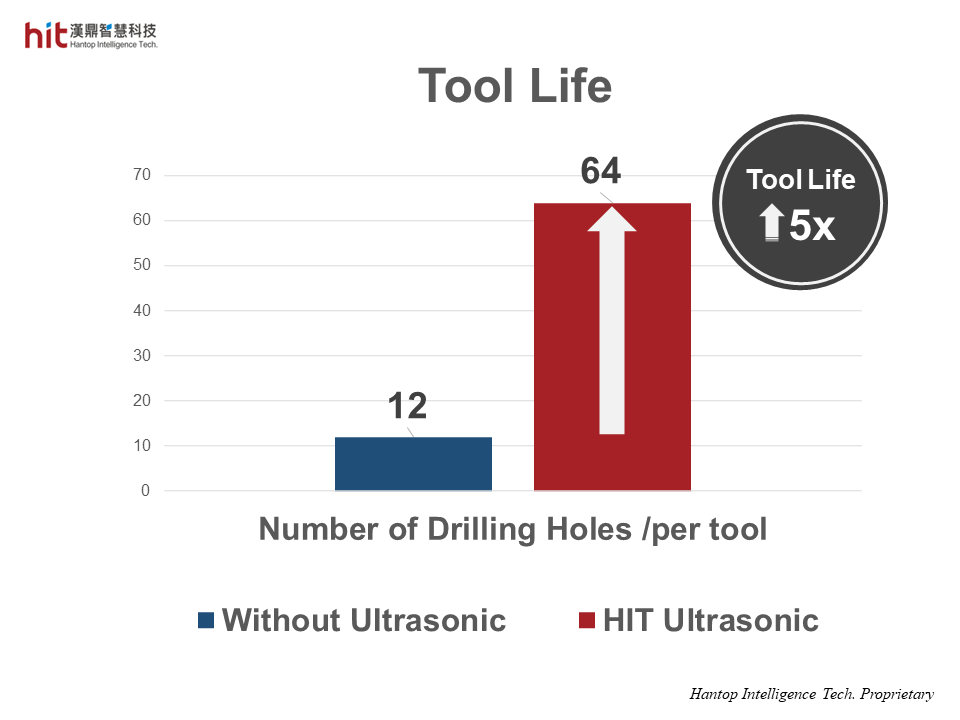
(Figure 3. HIT ultrasonic-assisted micro-drilling of Nickel Alloy Inconel 718 achieved 5x longer tool life)
HIT Achievements in Keyway Side Milling of Nickel Alloy (Inconel 718)
🕜 Efficiency - 2x higher
⚙️ Tool Life - 5x longer