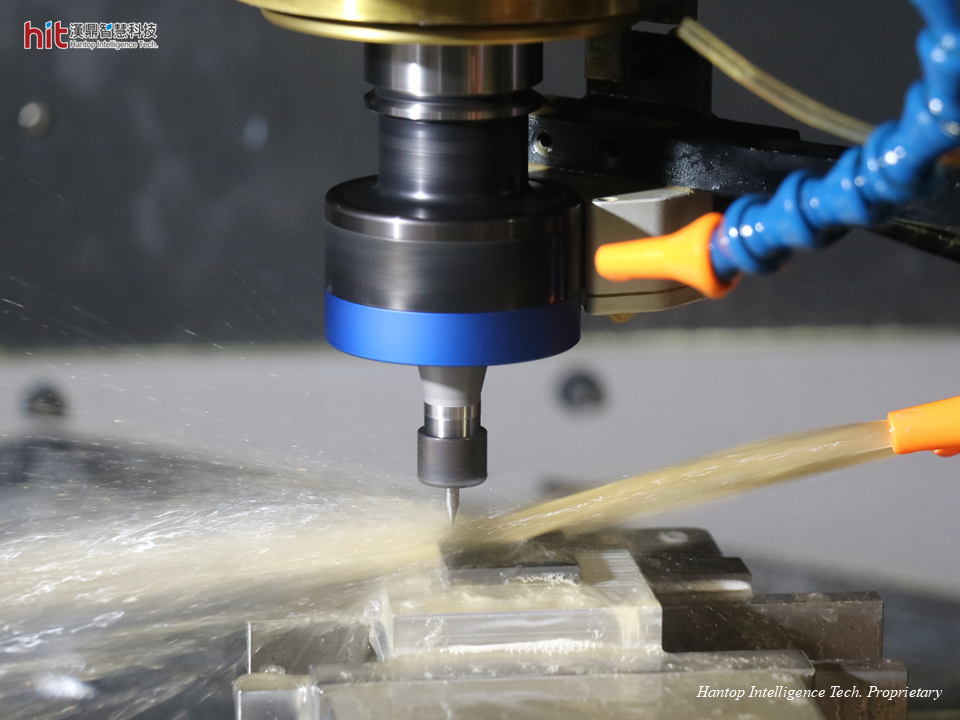
(圖1. 漢鼎HSKE40超音波模組輔助優化碳化矽SiC陶瓷PCD微鑽孔加工)
【漢鼎超音波】碳化矽(Sintered SiC)PCD微鑽孔加工:測試目標
針對碳化矽(Sintered SiC)的超音波HSKE40模組輔助PCD微鑽孔(盲孔)加工測試,目標為在提升整體加工效率,同時維持良好鑽孔品質並降低刀具磨耗,延長刀具壽命。
【漢鼎超音波】碳化矽(Sintered SiC)PCD微鑽孔加工:加工結果
碳化矽(Sintered SiC)PCD微鑽孔加工:加工效率
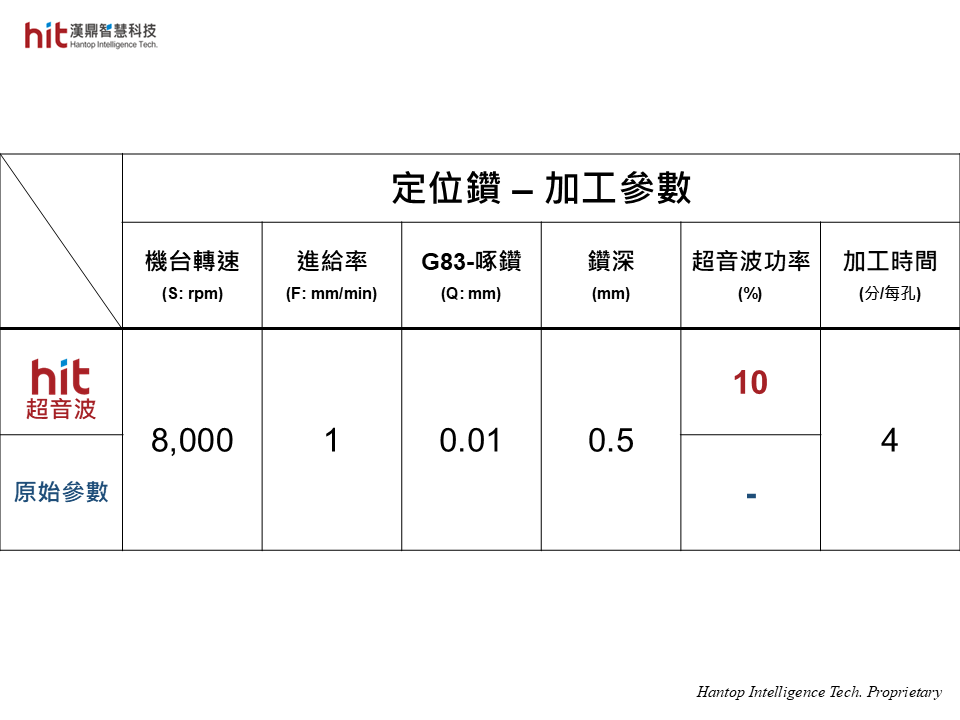
(圖2. 使用漢鼎超音波模組輔助優化碳化矽SiC陶瓷PCD微鑽孔加工, 定位鑽製程即可開啟超音波)
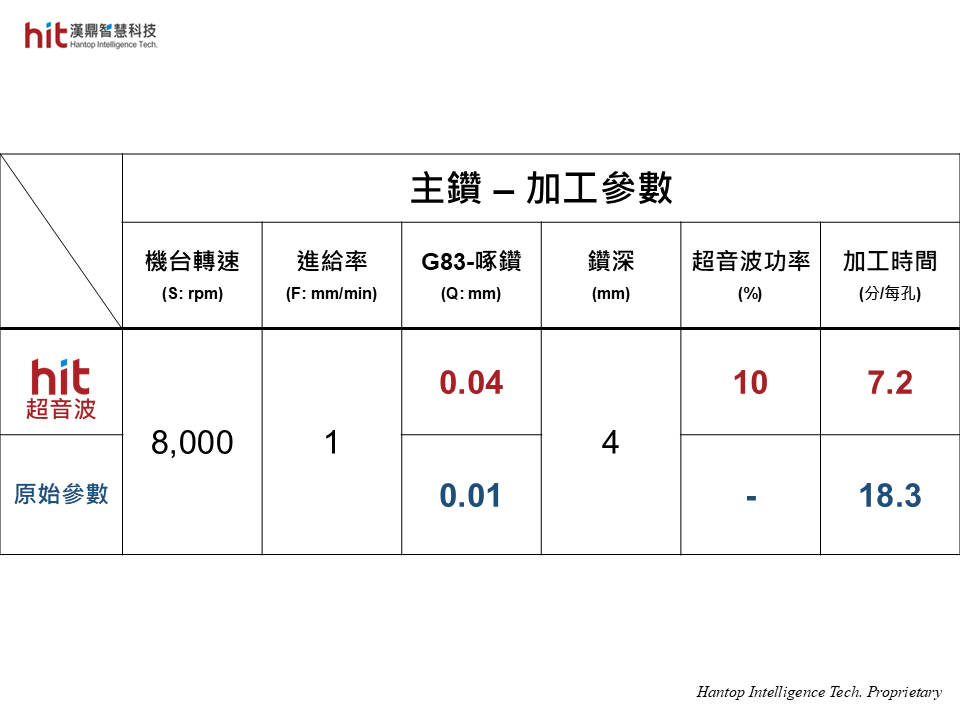
(圖3. 使用漢鼎超音波模組輔助優化碳化矽SiC陶瓷PCD微鑽孔加工, 主鑽製程中的啄鑽量-Q值可提升4倍, 達到整體加工效率的提升)
- 使用漢鼎超音波模組輔助優化碳化矽微鑽孔加工製程,搭配PCD鑽頭,在高頻率微振動下,幫助降低鑽削阻力。
- 在主鑽製程中,啄鑽量(Q值)可提升4倍(從0.01提升至0.04mm),使整體加工效率提升2.5倍,加工時間從每孔18.3分鐘,縮短至每孔7.2分鐘。
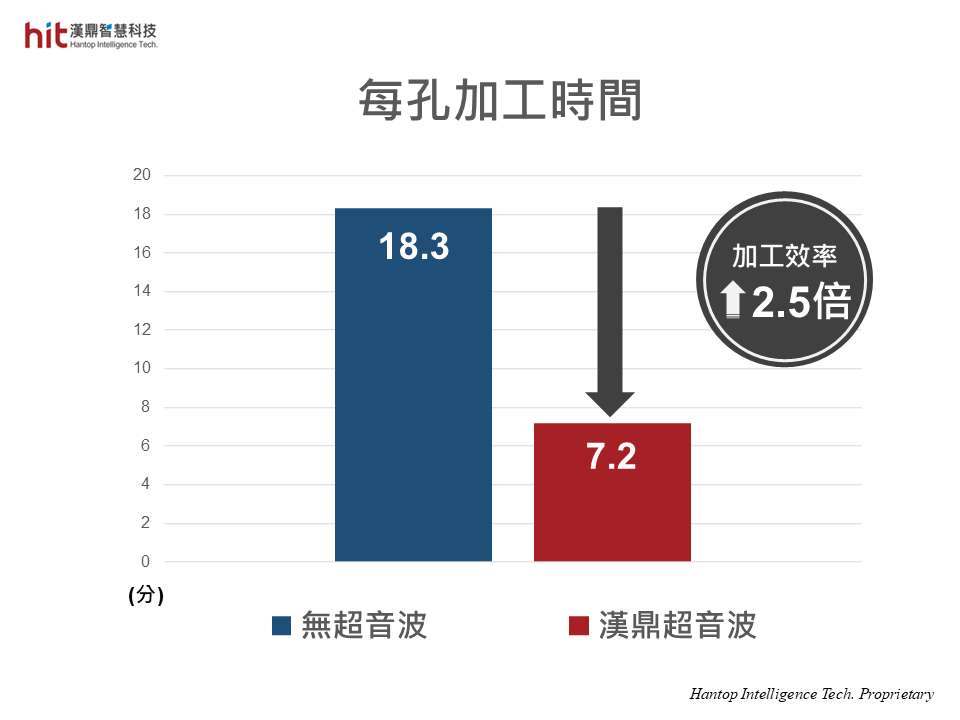
(圖4. 使用漢鼎超音波模組輔助優化碳化矽SiC陶瓷PCD微鑽孔加工, 幫助縮短每孔加工時間, 整體加工效率提升2.5倍)
碳化矽(Sintered SiC)PCD微鑽孔加工:鑽孔品質
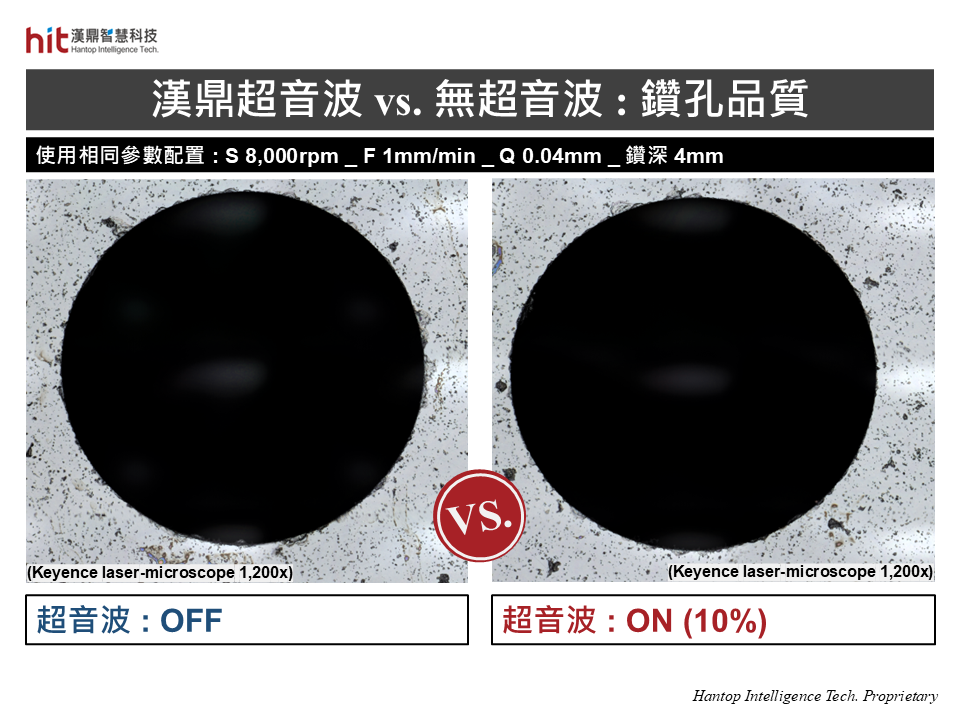
(圖5. 使用漢鼎超音波模組輔助優化碳化矽SiC陶瓷PCD微鑽孔加工, 加工參數優化後, 顯微鏡下脆裂邊尺寸極小)
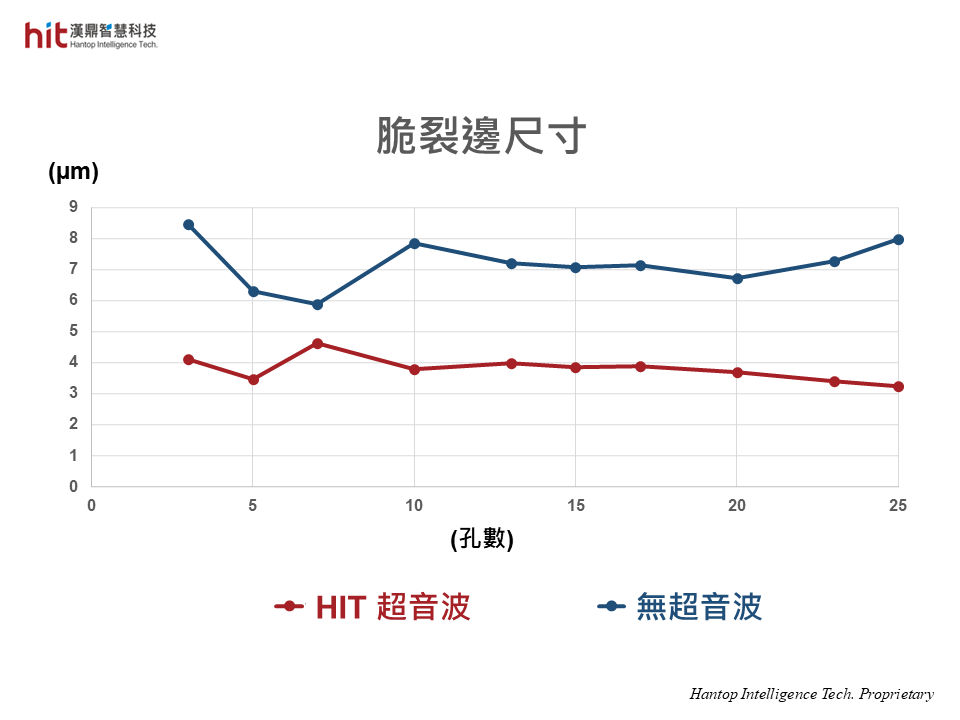
(圖6. 使用漢鼎超音波模組輔助優化碳化矽SiC陶瓷PCD微鑽孔加工, 每孔脆裂邊尺寸均小於5
µm)
- 使用漢鼎超音波,鑽削阻力的降低,使整體鑽孔製程更加穩定。
- 在加工效率提升2.5倍下,相較無超音波(使用相同參數配置-Q 0.04mm),完成25孔鑽孔.平均脆裂邊尺寸減小1.8倍,整體鑽孔品質提升近2倍。
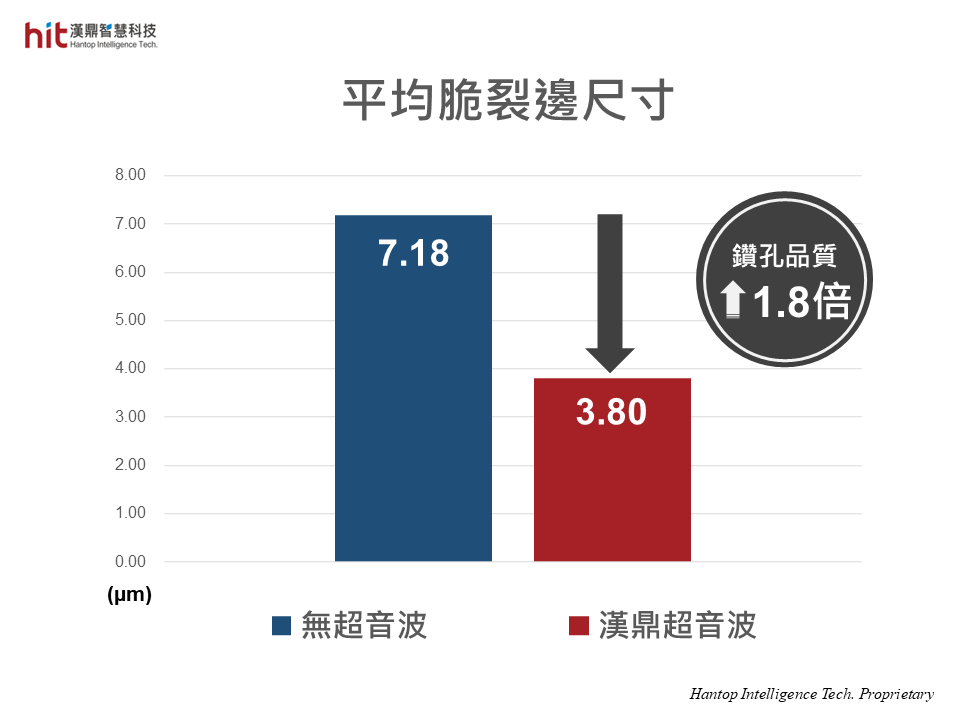
(圖7. 使用漢鼎超音波模組輔助優化碳化矽SiC陶瓷PCD微鑽孔加工, 平均脆裂邊尺寸減小, 整體鑽孔品質提升1.8倍)
碳化矽(Sintered SiC)PCD微鑽孔加工:刀具壽命
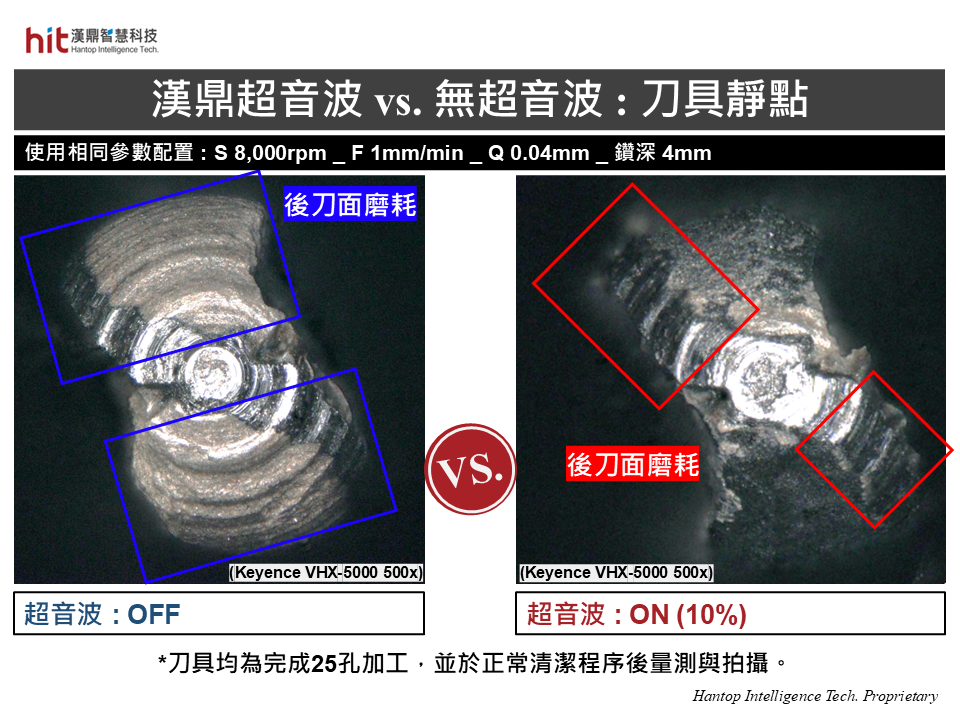
(圖8. 使用漢鼎超音波模組輔助優化碳化矽SiC陶瓷PCD微鑽孔加工, 從刀具靜點處觀察, 完成25孔加工後, 後刀面磨耗遠小於無超音波)
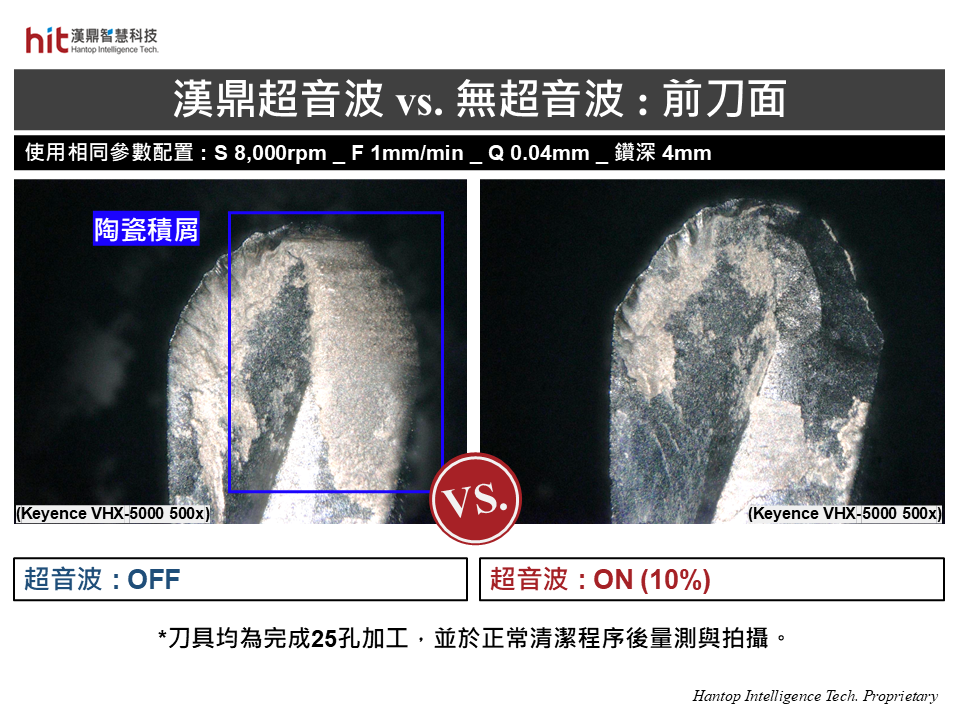
(圖9. 使用漢鼎超音波模組輔助優化碳化矽SiC陶瓷PCD微鑽孔加工, 從刀具前刀面觀察, 完成25孔加工後, 陶瓷積屑量遠小於無超音波)
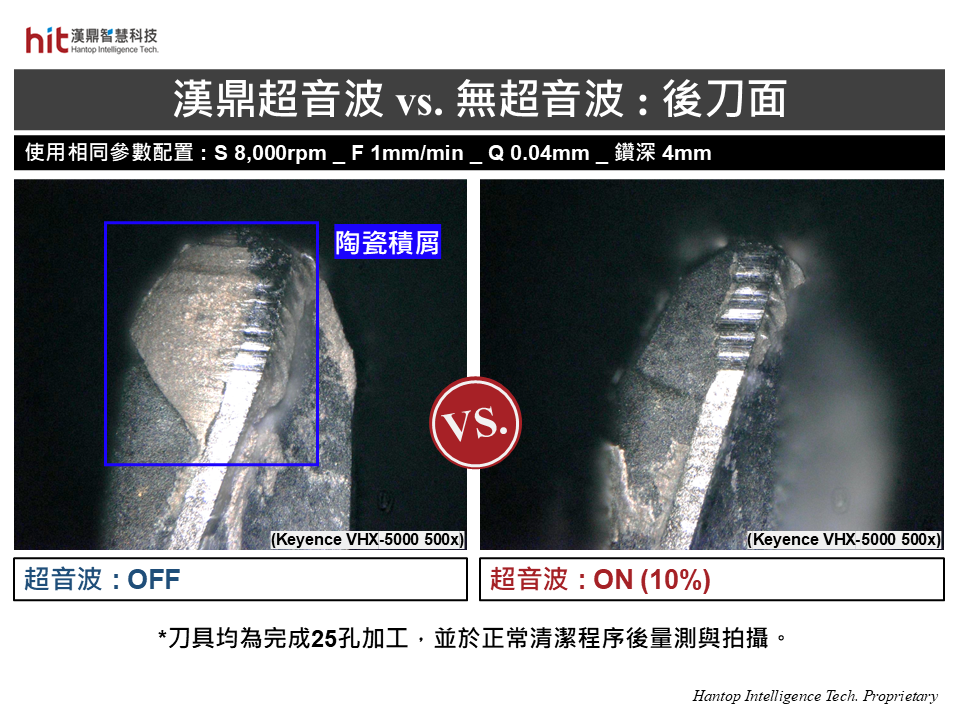
(圖10. 使用漢鼎超音波模組輔助優化碳化矽SiC陶瓷PCD微鑽孔加工, 從刀具後刀面觀察, 完成25孔加工後, 陶瓷積屑量遠小於無超音波)
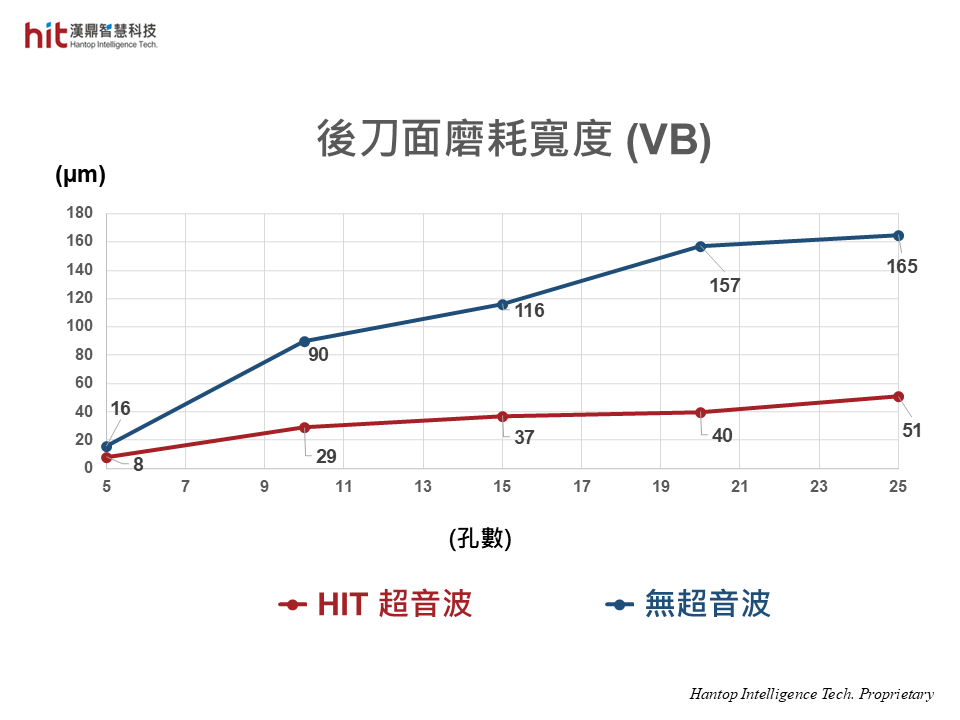
(圖11. 使用漢鼎超音波模組輔助優化碳化矽SiC陶瓷PCD微鑽孔加工, 後刀面磨耗寬度VB皆遠小於無超音波)
- 使用漢鼎超音波,高頻率微振動的切削機制,使切削液更易流入,排屑過程更順暢。
- 良好的排屑機制,以及鑽削阻力的降低,在加工效率提升2.5倍下,相較無超音波(使用相同參數配置-Q 0.04mm),刀具磨耗量減少3.2倍,有效延長刀具壽命。
【漢鼎超音波】碳化矽(Sintered SiC)PCD微鑽孔加工:超音波效益
🕜 加工效率 - 提升2.5倍,啄鑽量 (Q值) 提升4倍
📈 鑽孔品質 - 提升1.8倍,脆裂邊減小
⚙️ 刀具磨耗 - 減少3.2倍,良好排屑機制與鑽削阻力降低