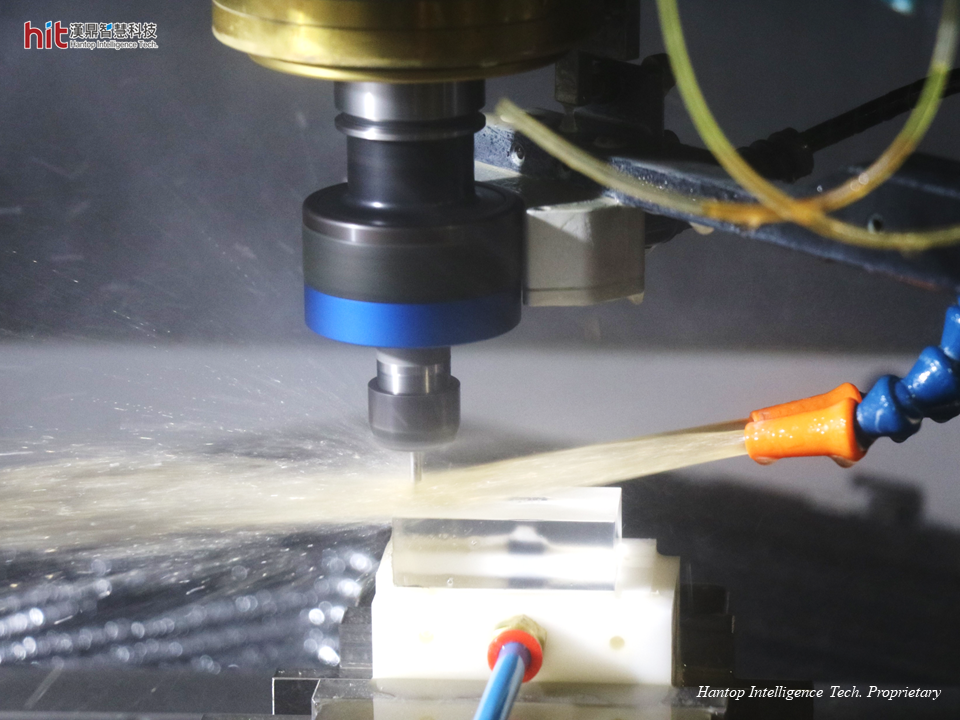
(Figure 1. HIT HSK-E40 ultrasonic machining module was used on micro-channel trochoidal machining of quartz glass)
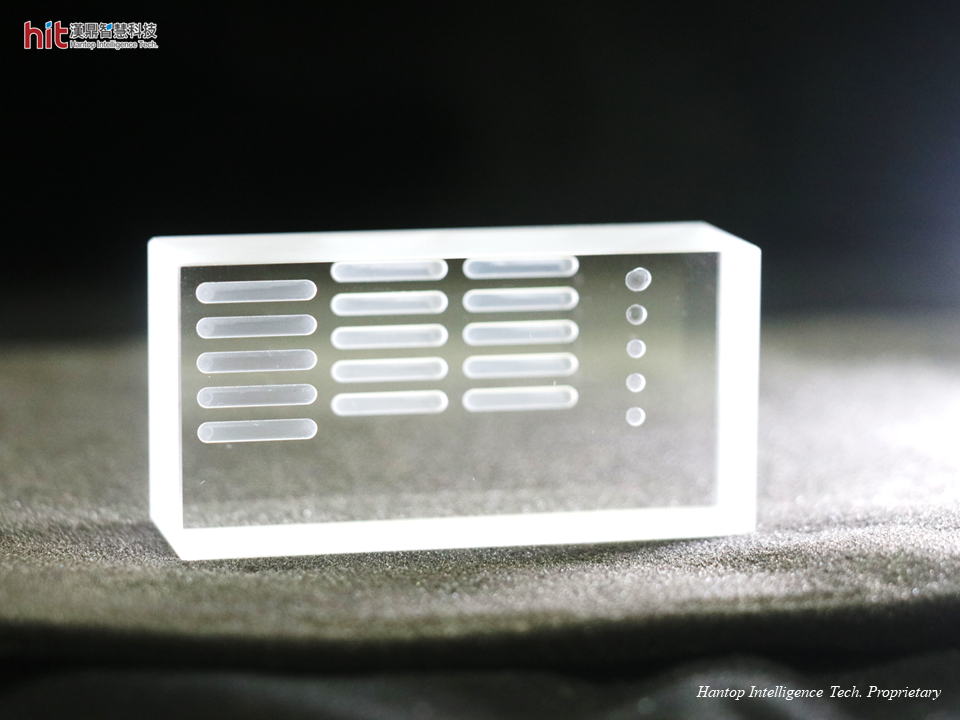
(Figure 2. HIT ultrasonic-assisted micro-channel trochoidal machining of quartz glass in the making of microfluidic devices)
HIT's Goal in Micro-channel Trochoidal Machining of Quartz Glass
Through the assistance of HIT ultrasonic-assisted machining technology, the goal is to reduce the size of edge-cracks around the micro-channels in the trochoidal grinding of quartz glass.
Ultrasonic-Assisted Trochoidal Grinding of Quartz Glass Machining Results
Quartz Glass Micro-channel Trochoidal Machining: Workpiece Quality
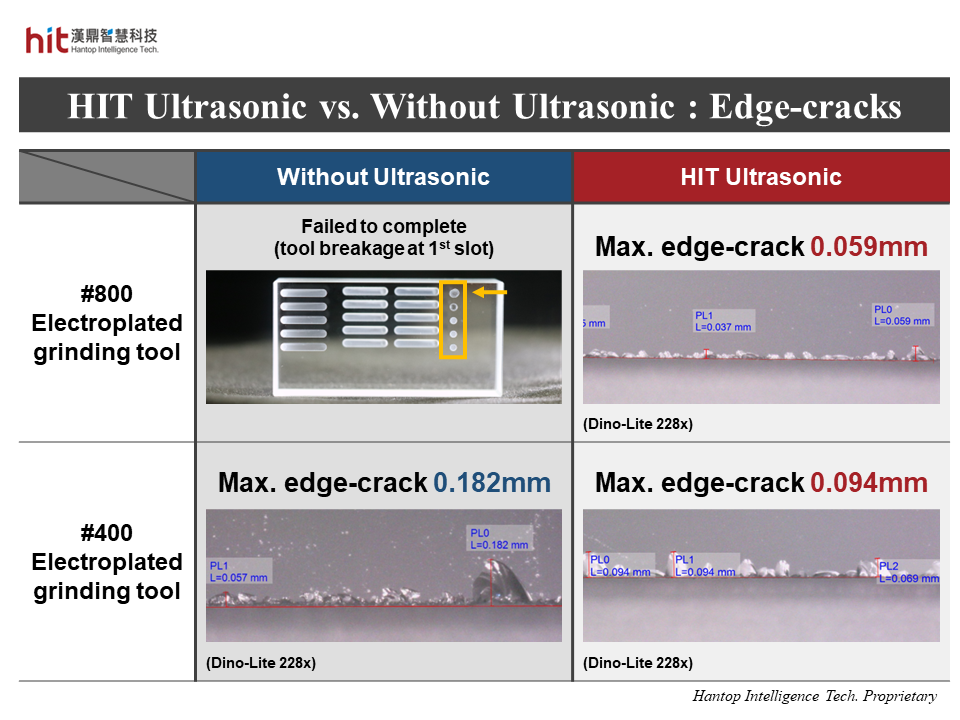
(Figure 3. HIT ultrasonic-assisted micro-channel trochoidal machining of quartz glass helped reduce the maximum size of edge-cracks (1x smaller and 2x smaller) by using #400 and #800 grinding tools respectively)
- The original process needed to go through by using #200, #400, and #800 grinding tools from roughing to finishing. With HIT ultrasonic, customer's requirement on workpiece quality can be achieved just by using #800 grinding tool.
- With HIT ultrasonic, high frequency micro-vibration helped reduce grinding forces. (Under the same machining parameters) The maximum size of edge-cracks was 1x smaller (from 0.182mm to 0.094mm) than that without ultrasonic, by using #400 grinding tool.
- (Under the same machining parameters) The maximum size of edge-cracks can be even smaller (down to 0.059mm) by using #800 grinding tool with HIT ultrasonic, while it failed to complete the machining process without ultrasonic due to tool breakage at the first slot.
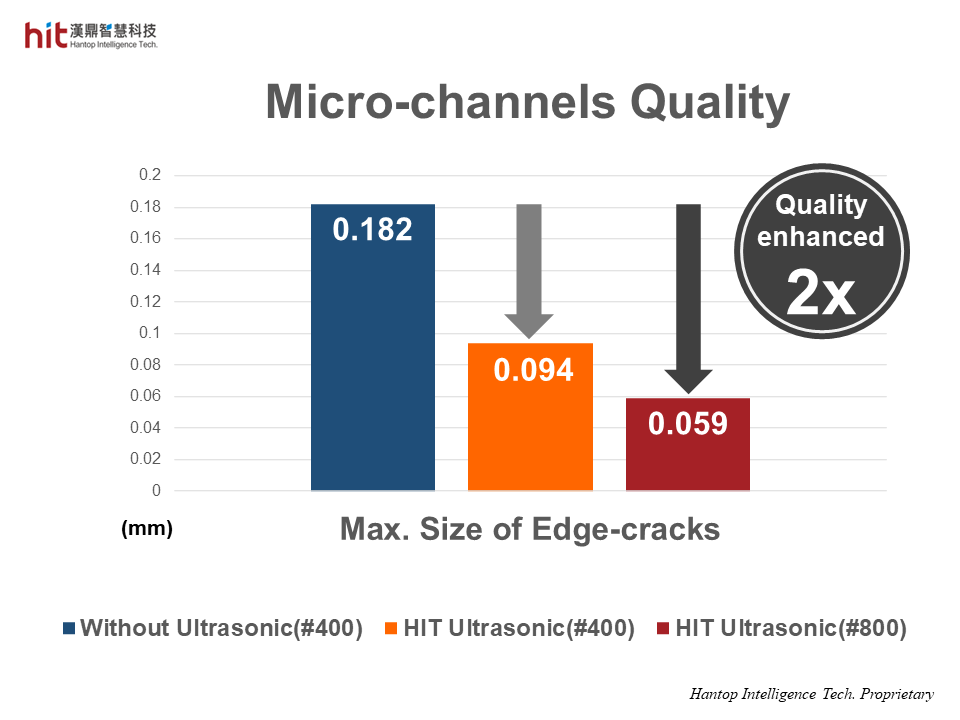
(Figure 4. HIT ultrasonic-assisted micro-channel trochoidal machining of quartz glass helped reduce the maximum size of edge-cracks, resulting in 2x improvement in workpiece quality)
Quartz Glass Micro-channel Trochoidal Machining: Tool Life
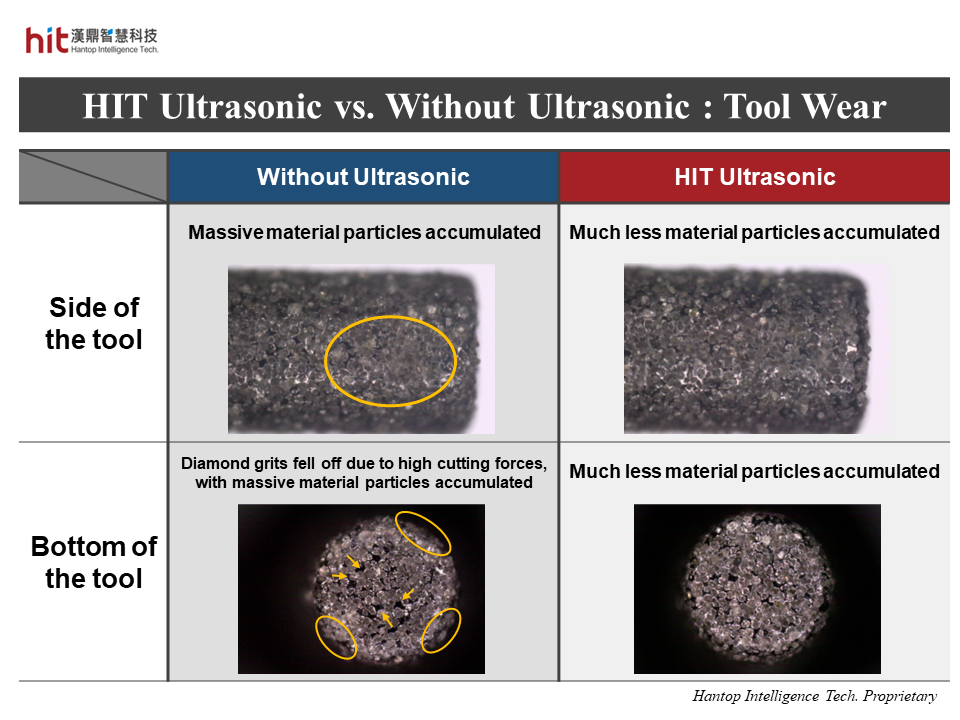
(Figure 5. HIT ultrasonic-assisted micro-channel trochoidal machining of quartz glass brought better particle flushing, preventing the tool from particles accumulation)
- With HIT ultrasonic, the tool constantly lifted from workpiece, which allowed for easier inflow of cutting fluid. Better particle flushing prevented the tool from serious material backfill. This not only reduced tool wear but also friction between tool and workpiece, which helped control and reduce grinding forces.
- (Under the same machining parameters) Without ultrasonic, the tool was in constant contact with workpiece, which made it hard for particle flushing. There were massive particles accumulated on both side and bottom of the tool. This weakened the tool's grinding ability and led to an increase in grinding forces. It not only impacted workpiece quality, but also caused serious tool wear.
HIT Ultrasonic Machining Technology on Micro-channel Trochoidal Machining of Quartz Glass Achievements
🕜 Efficiency - less manufacturing steps
📈 Quality - max. size of edge-cracks 2x smaller
⚙️ Tool Life - better particle flushing