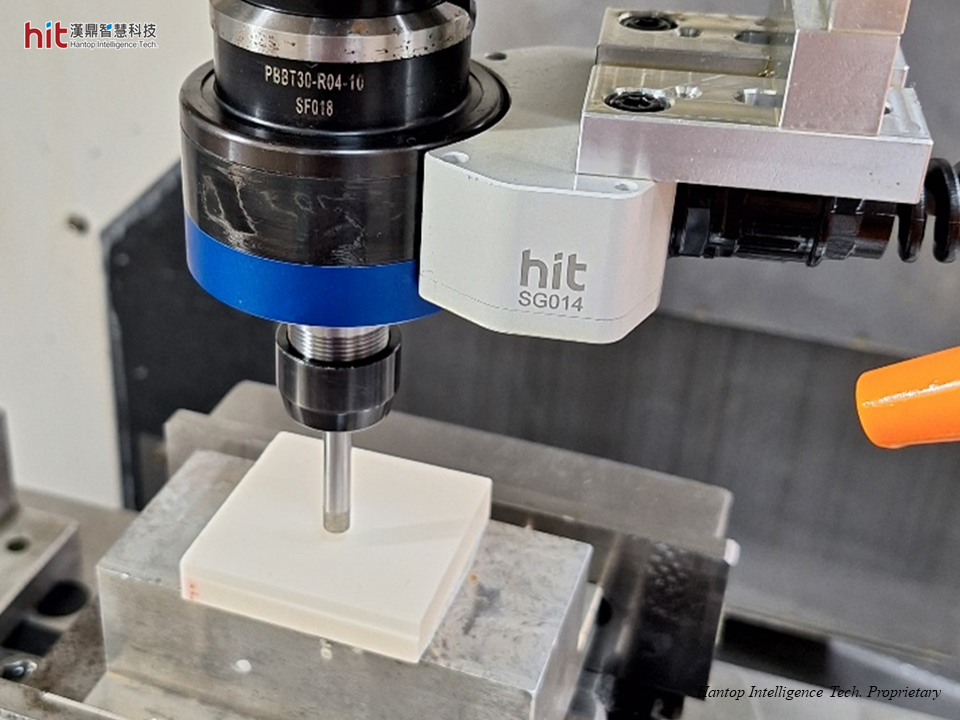
(Figure 1. HIT BT-30 ultrasonic machining module was used on side grinding of aluminum oxide ceramic)
HIT's Goal in Side Grinding of Aluminum Oxide (Al2O3) Ceramic
The goal is to do side grinding (rough grinding) of aluminum oxide ceramic with electroplated diamond grinding tool. With HIT ultrasonic, it was expected to reduce size of edge-cracks on the workpiece and to reduce tool wear.
Ultrasonic-Assisted Side Grinding of Aluminum Oxide (Al2O3) Ceramic: Machining Results
Aluminum Oxide (Al2O3) Ceramic Side Grinding: Workpiece Quality
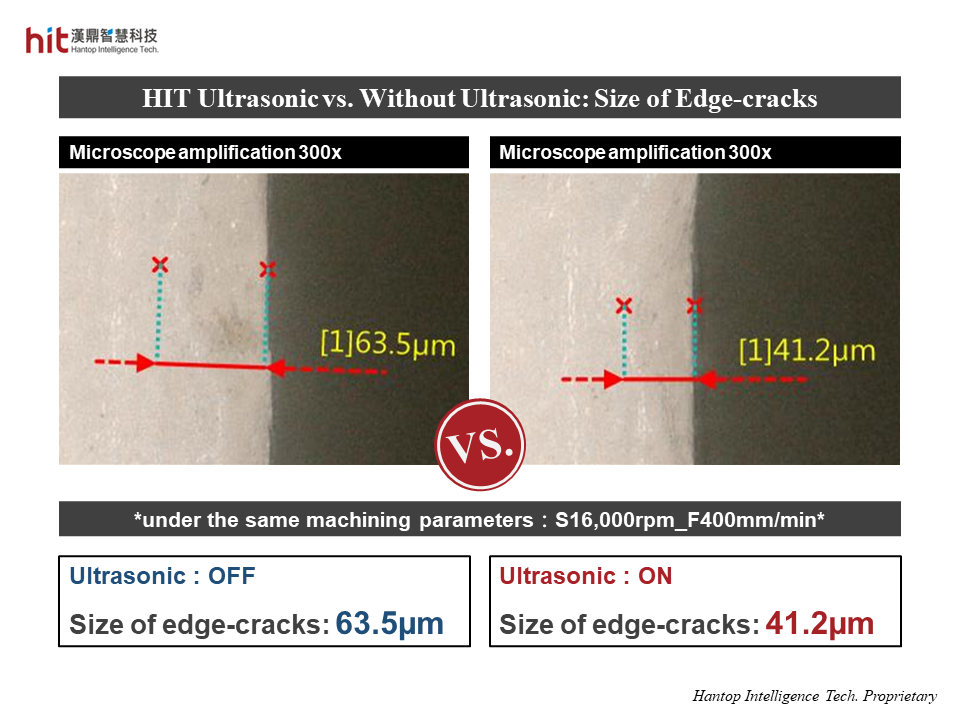
(Figure 2. HIT ultrasonic-assisted side grinding of aluminum oxide ceramic helped reduce 1.5x size of edge-cracks)
- With HIT ultrasonic, the high frequency micro-vibration helped reduce grinding forces.
- Under the same machining parameters (S 16,000rpm; F 400mm/min), the size of edge-cracks was 1.5x smaller than that without ultrasonic.
Aluminum Oxide (Al2O3) Ceramic Side Grinding: Tool Life
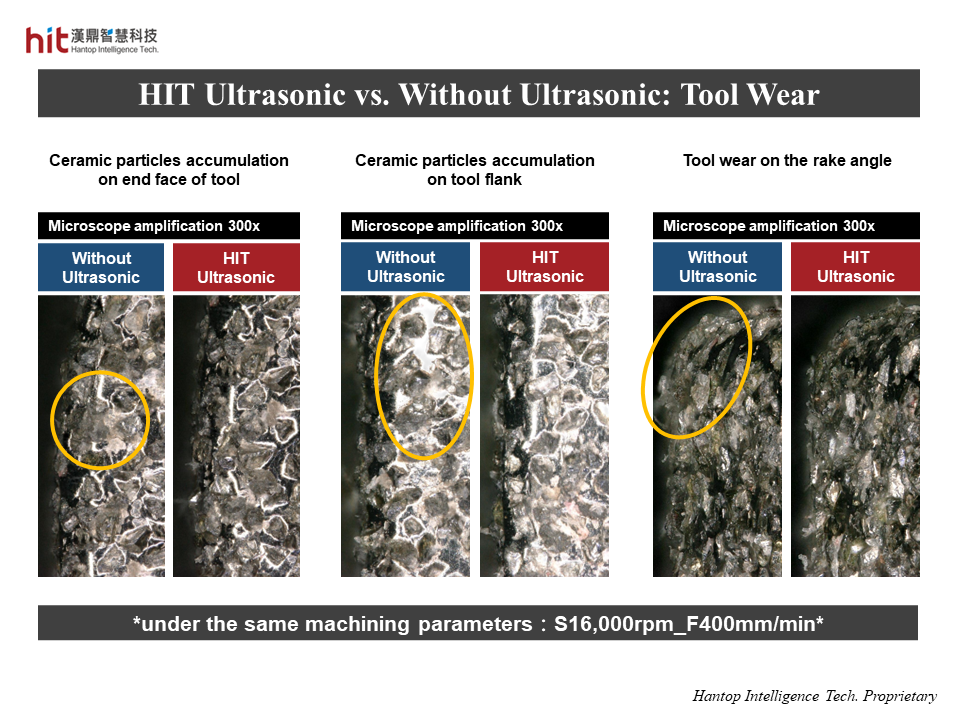
(Figure 3. HIT ultrasonic-assisted side grinding of aluminum oxide ceramic brought better particle flushing, resulting in reduced tool wear)
- There would be increasing grinding forces if massive ceramic dust was accumulated on the electroplated grinding tool. This would not only accelerate tool wear but also damage the surface quality of workpiece.
- With HIT ultrasonic, the high frequency micro-vibration led to better ceramic particle flushing. The prevention of ceramic particle accumulation helped reduce grinding forces and tool wear.
HIT Ultrasonic Technology Achievements in Side Grinding of Aluminum Oxide (Al2O3) Ceramic
📈 Quality - size of edge-cracks 1.5x smaller
⚙️ Tool Life - prevention of ceramic particle accumulation