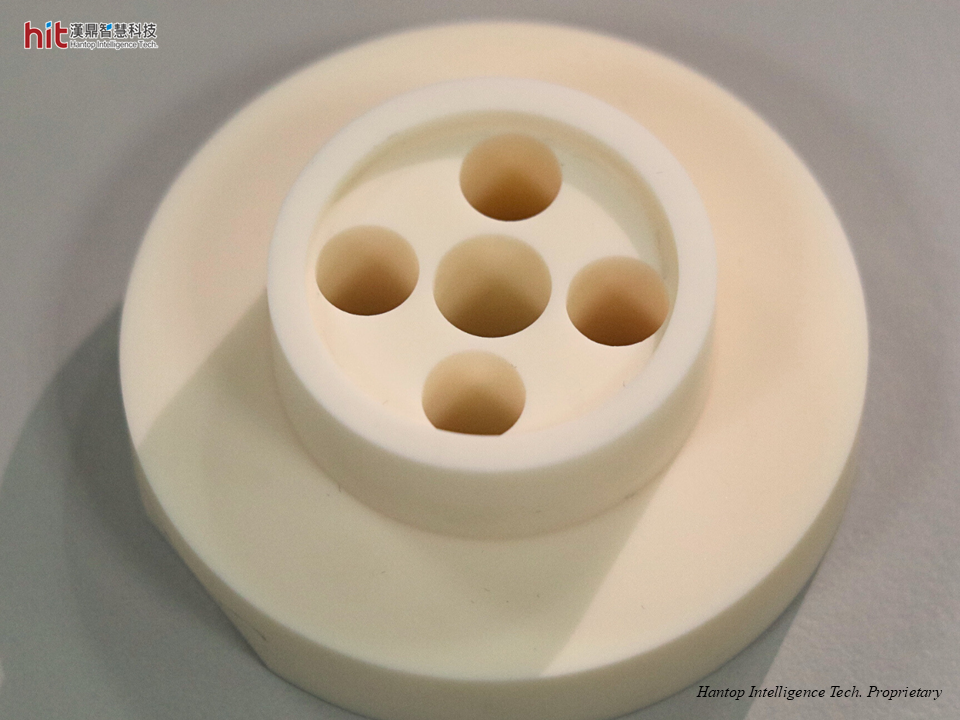
(Figure 1. HIT HSK-E40 ultrasonic machining module with HIT ultrasonic electroplated diamond grinding tool were used on aluminum oxide ceramic profile grinding process)
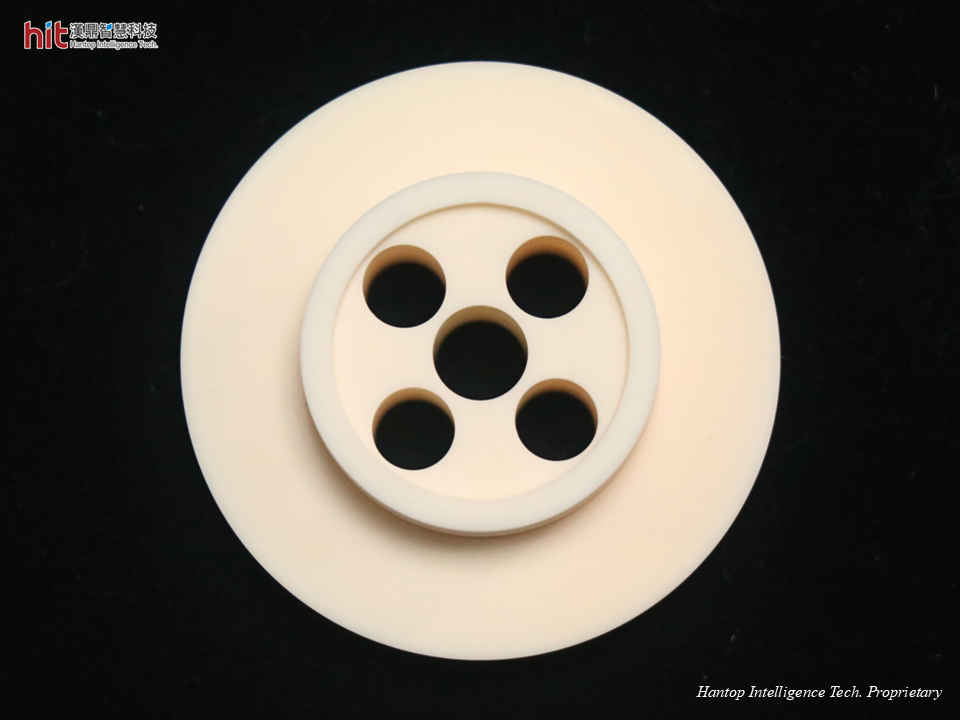
(Figure 2. HIT HSK-E40 ultrasonic machining module with HIT ultrasonic electroplated diamond grinding tool were used on aluminum oxide ceramic profile grinding process)
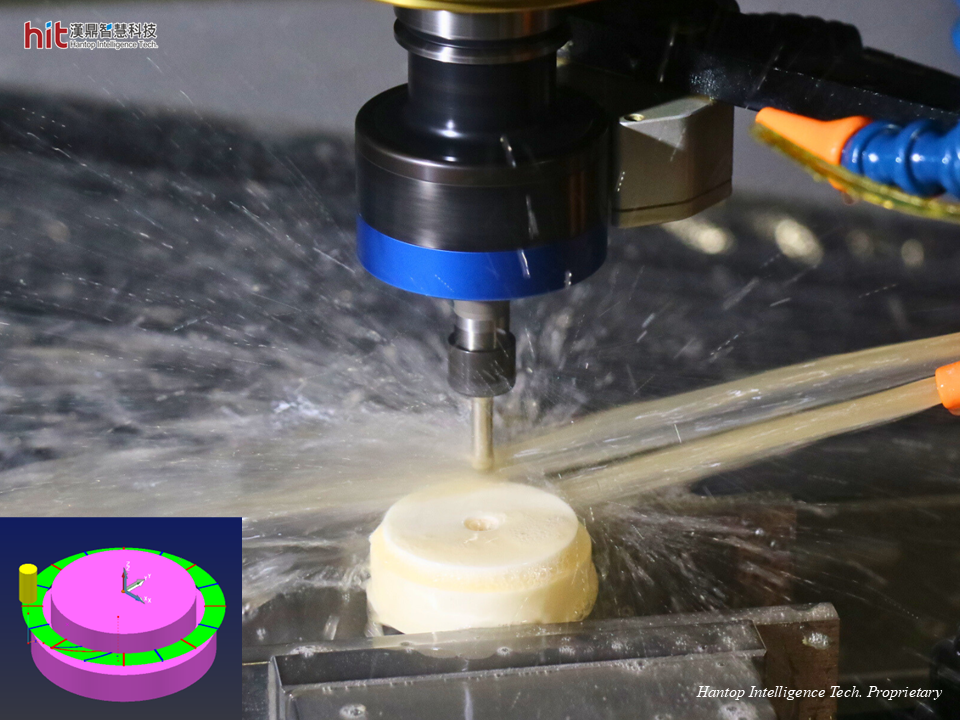
(Figure 3. HIT HSK-E40 ultrasonic machining module with HIT ultrasonic electroplated diamond grinding tool were used on aluminum oxide ceramic profile grinding -
External Cylindrical Grinding feature)
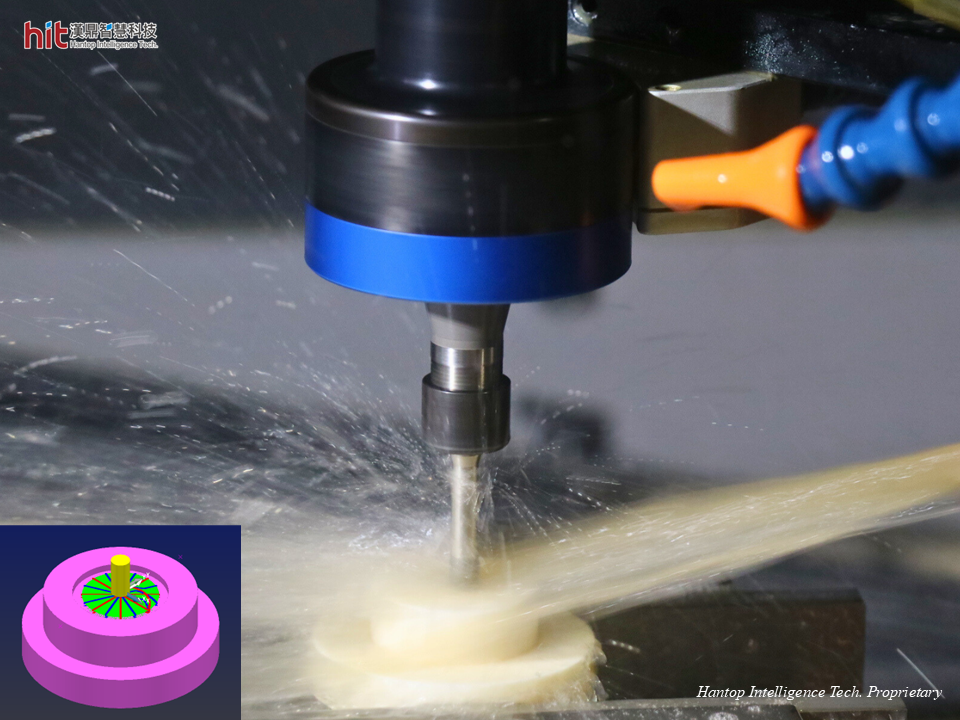
(Figure 4. HIT HSK-E40 ultrasonic machining module with HIT ultrasonic electroplated diamond grinding tool were used on aluminum oxide ceramic profile grinding -
Internal Bottom Grinding feature)
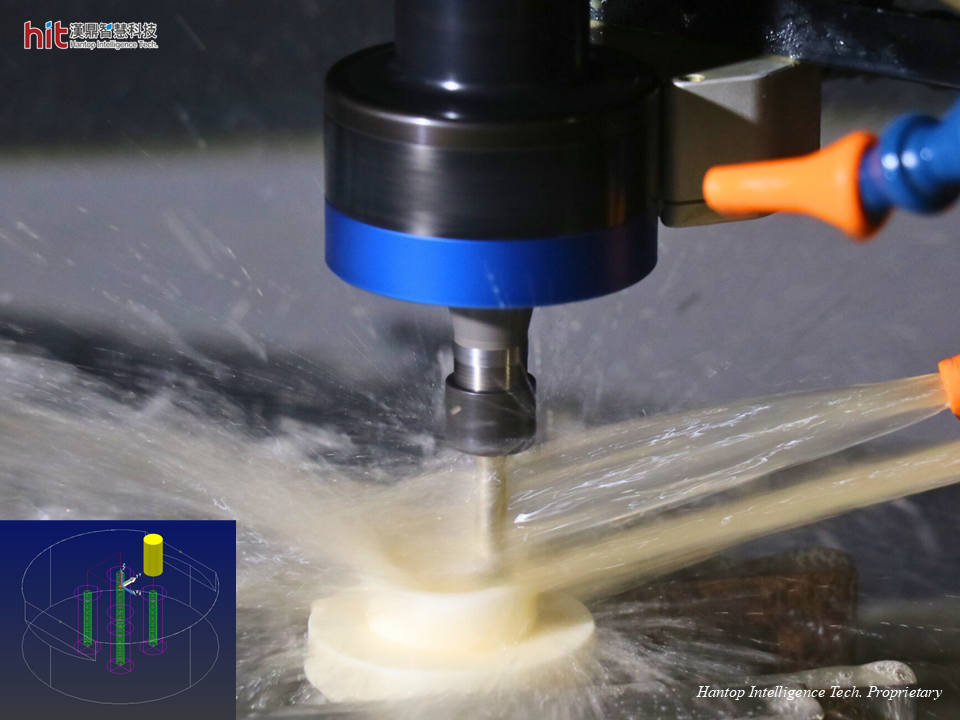
(Figure 5. HIT HSK-E40 ultrasonic machining module with HIT ultrasonic electroplated diamond grinding tool were used on aluminum oxide ceramic profile grinding -
Through-hole Grinding feature)
HIT's Goal in Profile Grinding of Aluminum Oxide (Al2O3) Ceramic
The goal is to do profile grinding on aluminum oxide ceramic with HIT ultrasonic-assisted machining technology on CNC machine with HIT ultrasonic electroplated diamond grinding tool. It is expected to enhance machining efficiency and prolong tool life on the premise of maintaining great workpiece quality.
Ultrasonic-Assisted Profile Grinding of Aluminum Oxide (Al2O3) Ceramic: Machining Results
Profile Grinding of Aluminum Oxide (Al2O3) Ceramic: Machining Efficiency
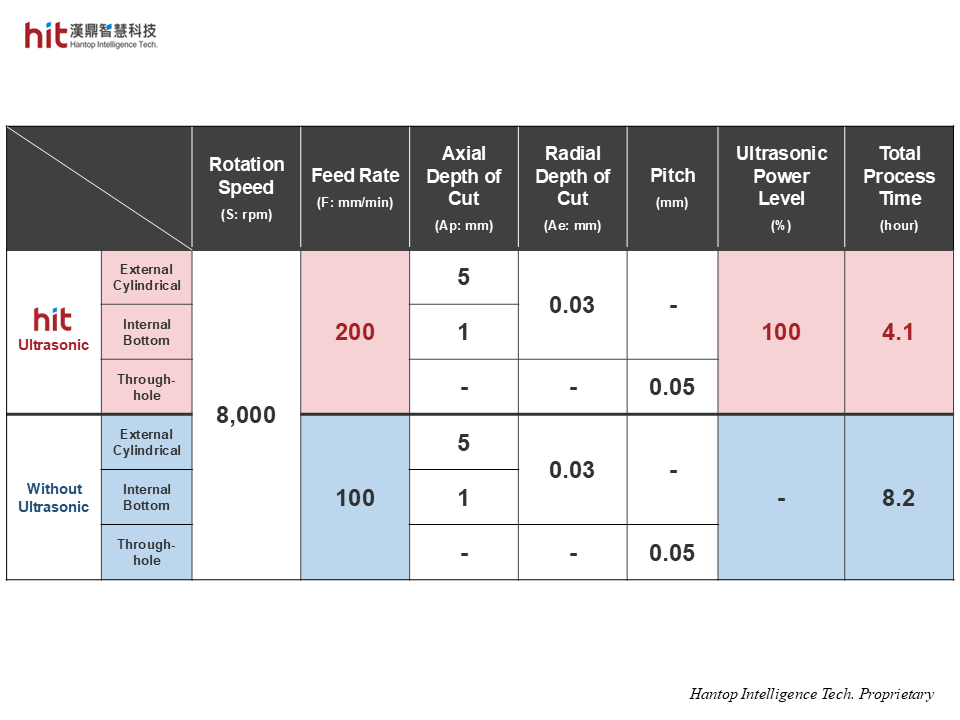
(Figure 6. HIT HSK-E40 ultrasonic machining module with HIT ultrasonic electroplated diamond grinding tool were used on aluminum oxide ceramic profile grinding, and the feed rate can be raised 2x faster)
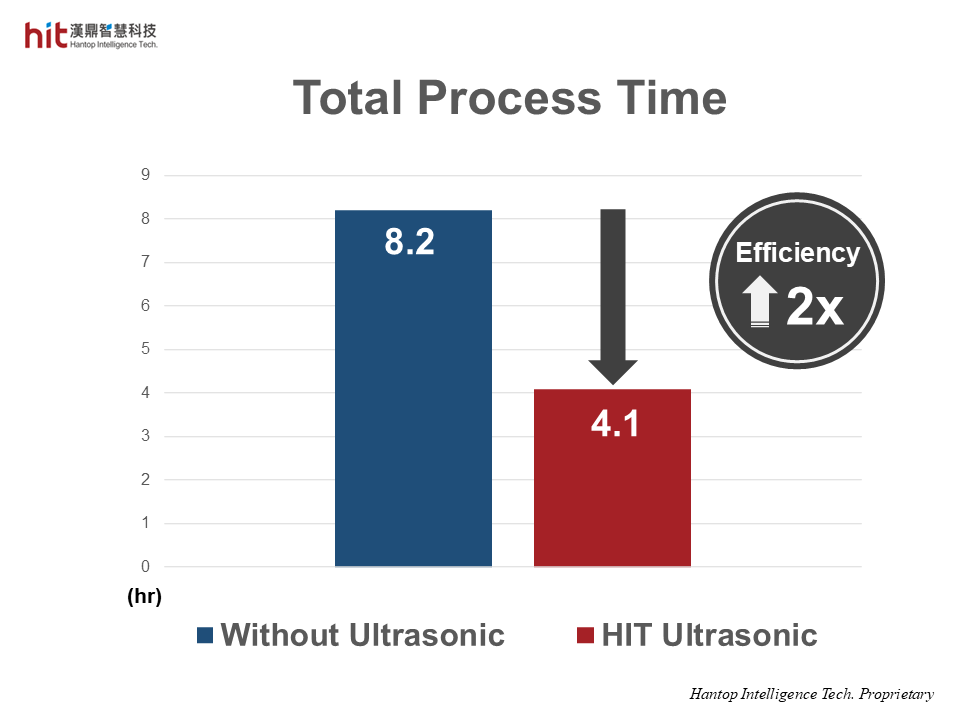
(Figure 7. HIT HSK-E40 ultrasonic machining module with HIT ultrasonic electroplated diamond grinding tool were used on aluminum oxide ceramic profile grinding, and the machining efficiency was 2x higher)
- With HIT ultrasonic, along with HIT ultrasonic electroplated diamond grinding tool, the high frequency micro-vibration allowed for easier removal of ceramic particles (material debris) from the grinding tool, which helped reduce grinding force.
- On the premise of maintaining great workpiece quality, feed rate can be raised 2x faster compared to that without ultrasonic.
- The total process time went from 8 hours to 4 hours, which brought 2x higher machining efficiency.
Profile Grinding of Aluminum Oxide (Al2O3) Ceramic: Workpiece Quality
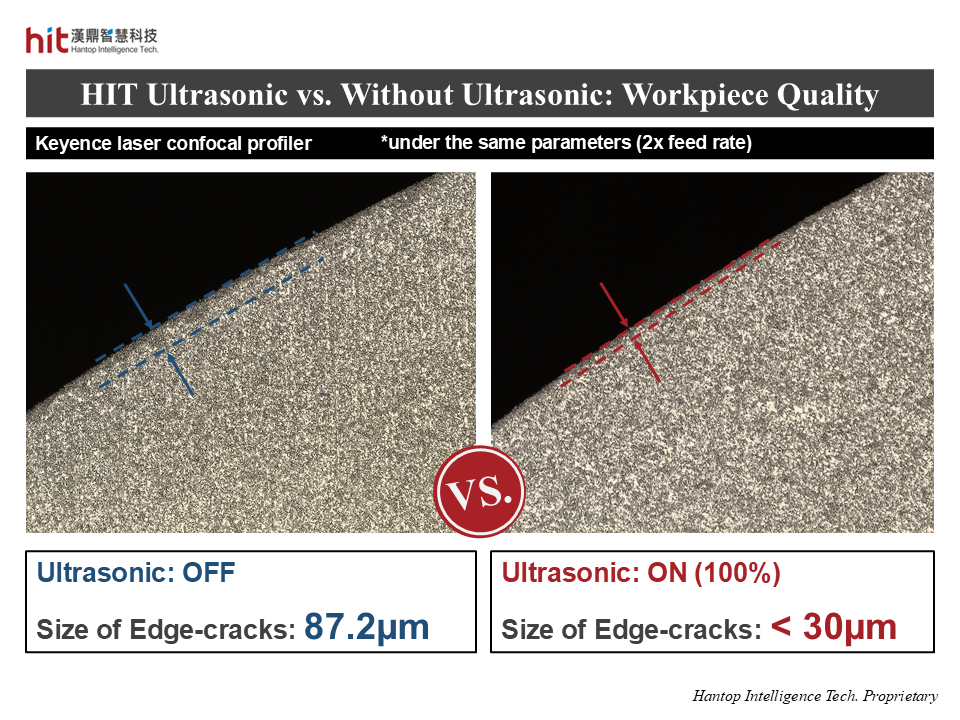
(Figure 8. HIT HSK-E40 ultrasonic machining module with HIT ultrasonic electroplated diamond grinding tool were used on aluminum oxide ceramic profile grinding, and the size of edge-cracks can be reduced nearly 3x smaller)
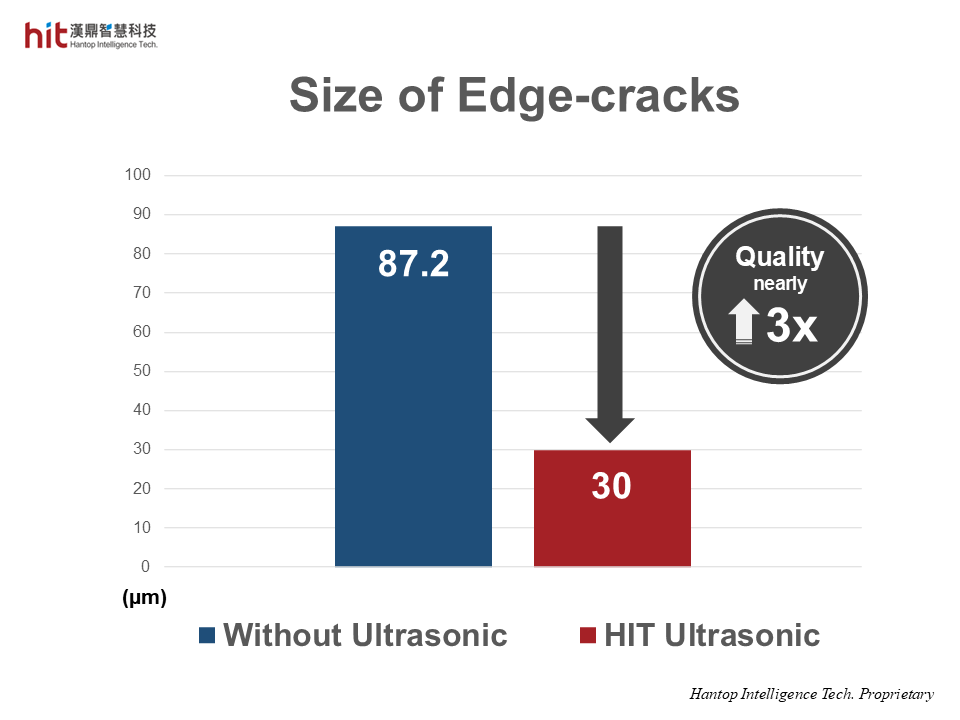
(Figure 9. HIT HSK-E40 ultrasonic machining module with HIT ultrasonic electroplated diamond grinding tool were used on aluminum oxide ceramic profile grinding, and the workpiece quality was nearly 3x better)
- With HIT ultrasonic, along with HIT ultrasonic electroplated diamond grinding tool, the high frequency micro-vibration allowed for easier removal of ceramic particles.
- Reduction in grinding force and tool wear stabilized the entire grinding process. This helped restrain the formation of edge-cracks.
- The workpiece quality was thus nearly 3x better than that without ultrasonic.
Profile Grinding of Aluminum Oxide (Al2O3) Ceramic: Tool Life
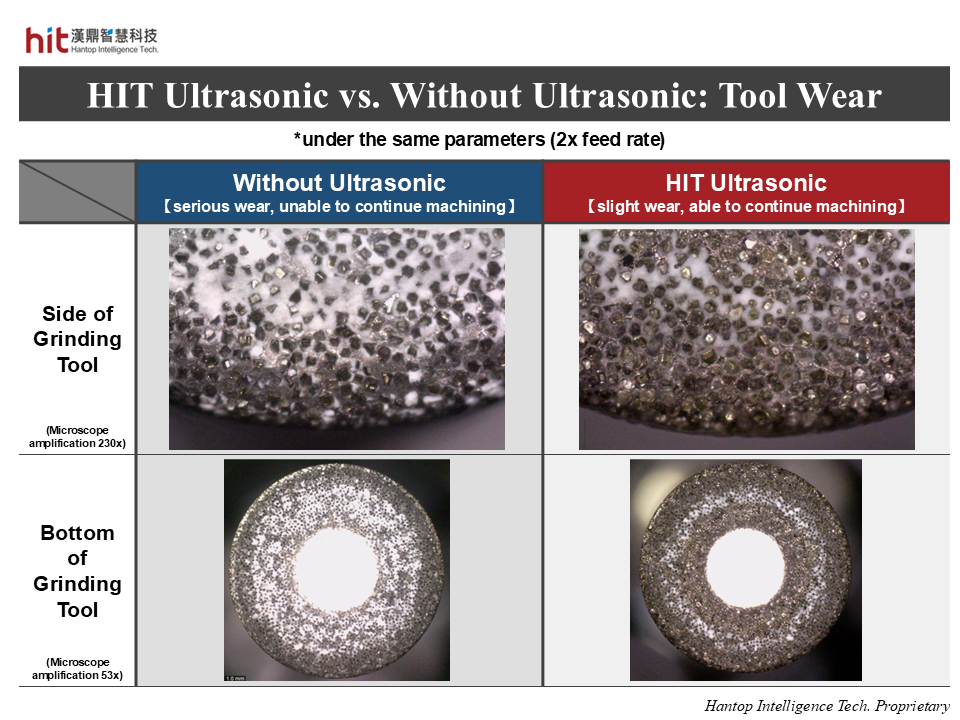
(Figure 10. HIT HSK-E40 ultrasonic machining module with HIT ultrasonic electroplated diamond grinding tool were used on aluminum oxide ceramic profile grinding, which helped greatly reduce tool wear)
- With HIT ultrasonic, along with HIT ultrasonic electroplated diamond grinding tool, the high frequency micro-vibration allowed for easier removal of ceramic particles.
- Both side and bottom areas of the grinding tool had much less accumulation of ceramic particles compared to that without ultrasonic, and the tool was able to continue machining after completing one ceramic workpiece.
- Great improvement in tool wear helped reduce grinding force. This not only contributed to great workpiece quality, but also provided an opportunity to increase the machining efficiency.
HIT Ultrasonic Machining Technology Achievements in Profile Grinding of Aluminum Oxide (Al2O3) Ceramic
(with HIT Ultrasonic Electroplated Diamond Grinding Tool)
🕜 Efficiency - 2x higher
📈 Quality - nearly 3x better
⚙️ Great Reduction in Tool Wear