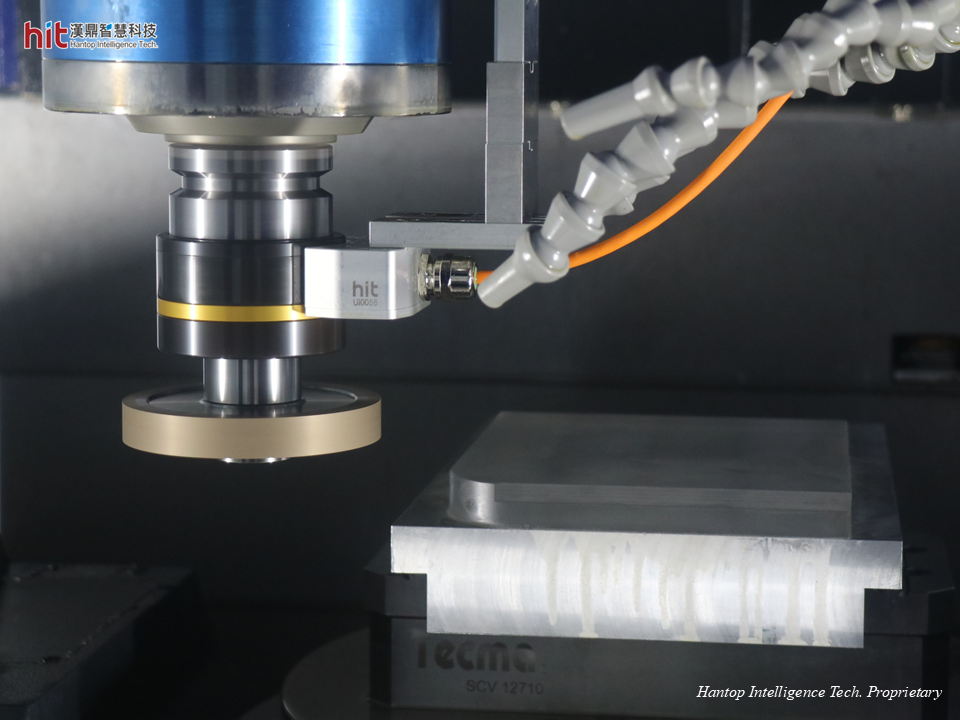
(Figure 1. HIT HBT-40 ultrasonic grinding wheel toolholder module was used on side grinding of quartz glass)
HIT's Goal in (Rough) Side Grinding of Quartz Glass with D100-Grinding Wheel Toolholder
Through the assistance of HIT ultrasonic-assisted machining technology with the new product - Ultrasonic Grinding Wheel Toolholder, the goal is to enhance machining efficiency and material removal rate, while maintaining great workpiece quality and stable tool life.
Ultrasonic-Assisted (Rough) Side Grinding of Quartz Glass with D100-Grinding Wheel Toolholder: Machining Results
(Rough) Side Grinding of Quartz Glass with D100-Grinding Wheel Toolholder: Machining Efficiency
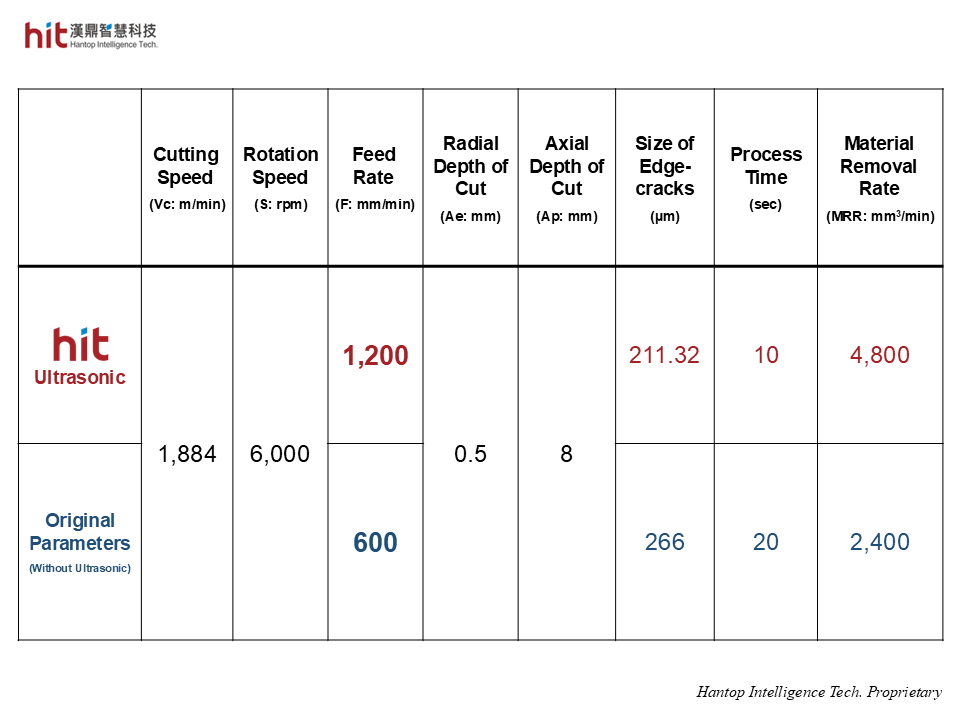
(Figure 2. with HIT new product HBT-40 ultrasonic grinding wheel toolholder module, feed rate can be raised 2x higher than the original parameters)
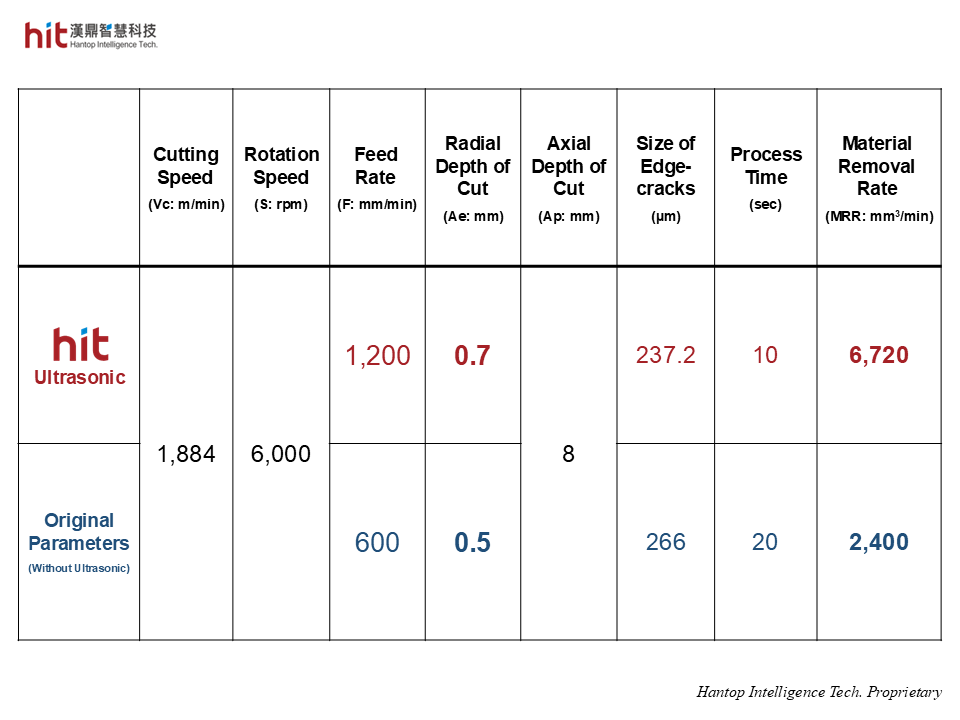
(Figure 3. with HIT new product HBT-40 ultrasonic grinding wheel toolholder module, radial depth of cut can be further enhanced, which brought nearly 3x higher material removal rate)
- To optimize the (rough) side grinding process of quartz glass with HIT ultrasonic module, the high frequency micro-vibration helped reduce grinding force. This allowed feed rate to be enhanced 2x higher, which reduced half of the total process time (from 20 seconds to 10 seconds).
- Radial depth of cut (Ae) can be further enhanced on the premise of stable workpiece quality. This then allowed MRR (Material Removal Rate) to be enhanced nearly 3x higher.
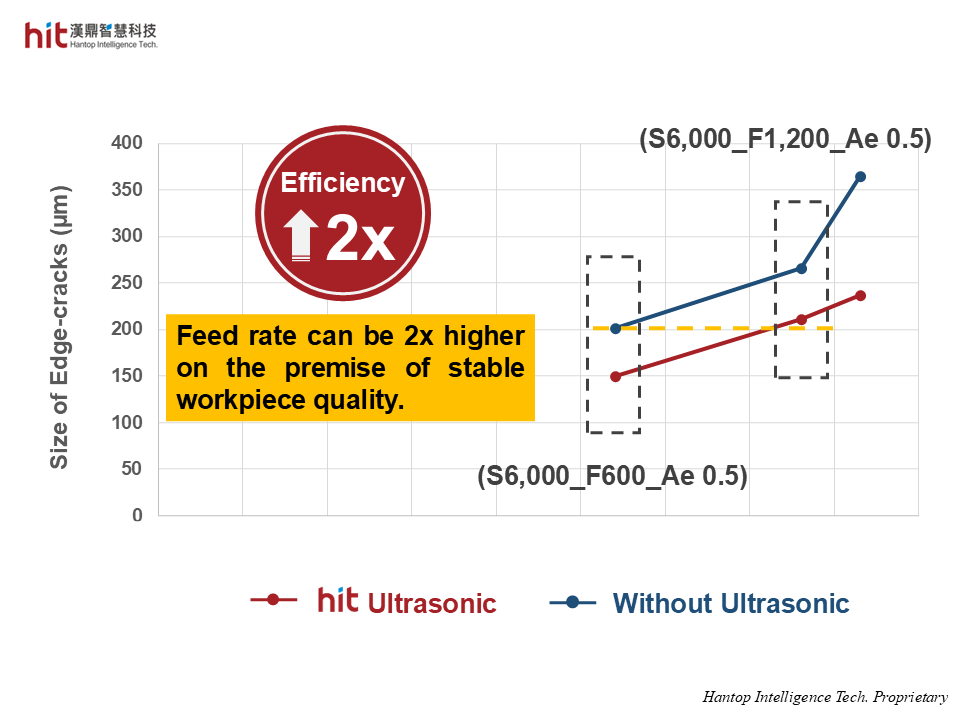
(Figure 4. with HIT new product HBT-40 ultrasonic grinding wheel toolholder module, overall machining efficiency can be 2x higher on the premise of stable workpiece quality)
(Rough) Side Grinding of Quartz Glass with D100-Grinding Wheel Toolholder: Workpiece Quality
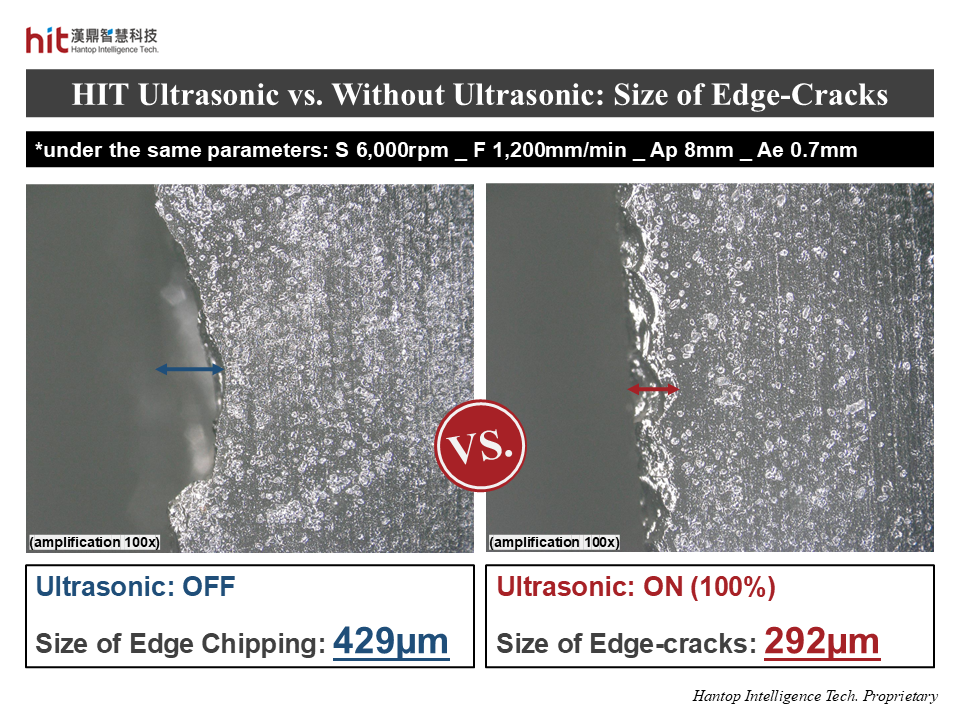
(Figure 5. with HIT new product HBT-40 ultrasonic grinding wheel toolholder module, size of edge-cracks can be smaller than that without ultrasonic)
- To optimize the (rough) side grinding process of quartz glass with HIT ultrasonic module, the high frequency micro-vibration helped reduce grinding force.
- Under 2x higher efficiency, the size of edge-cracks was stable (stable output of ultrasonic vibration amplitude). Under the same parameters, the size of edge-cracks was around 1.5x smaller than that without ultrasonic.
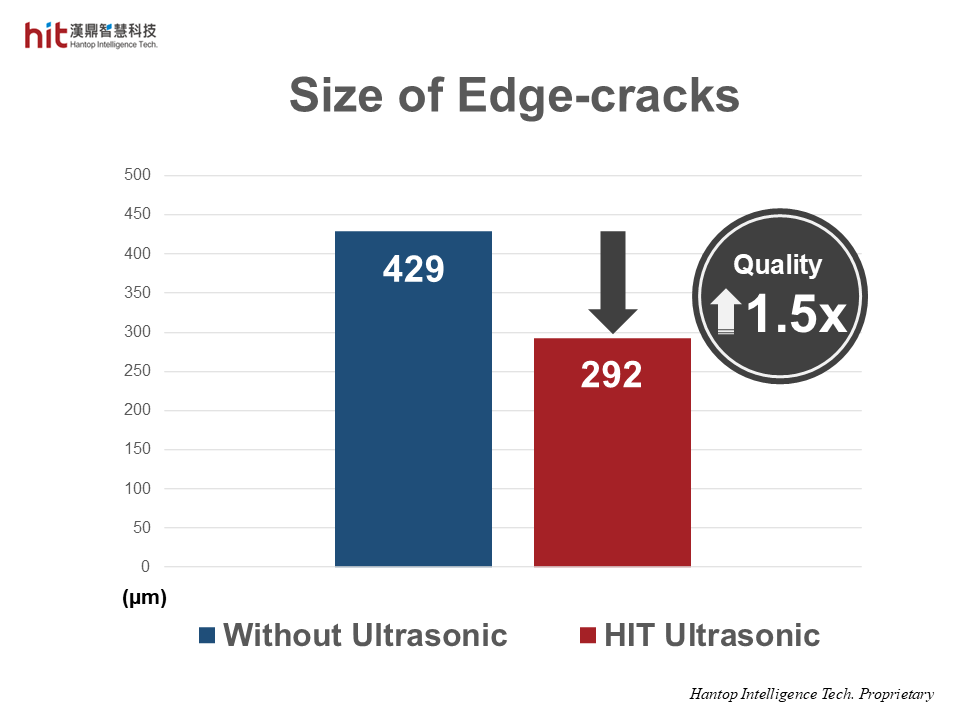
(Figure 6. with HIT new product HBT-40 ultrasonic grinding wheel toolholder module, it helped reduce the size of edge-cracks, which brought 1.5x better workpiece quality)
(Rough) Side Grinding of Quartz Glass with D100-Grinding Wheel Toolholder: Tool Life
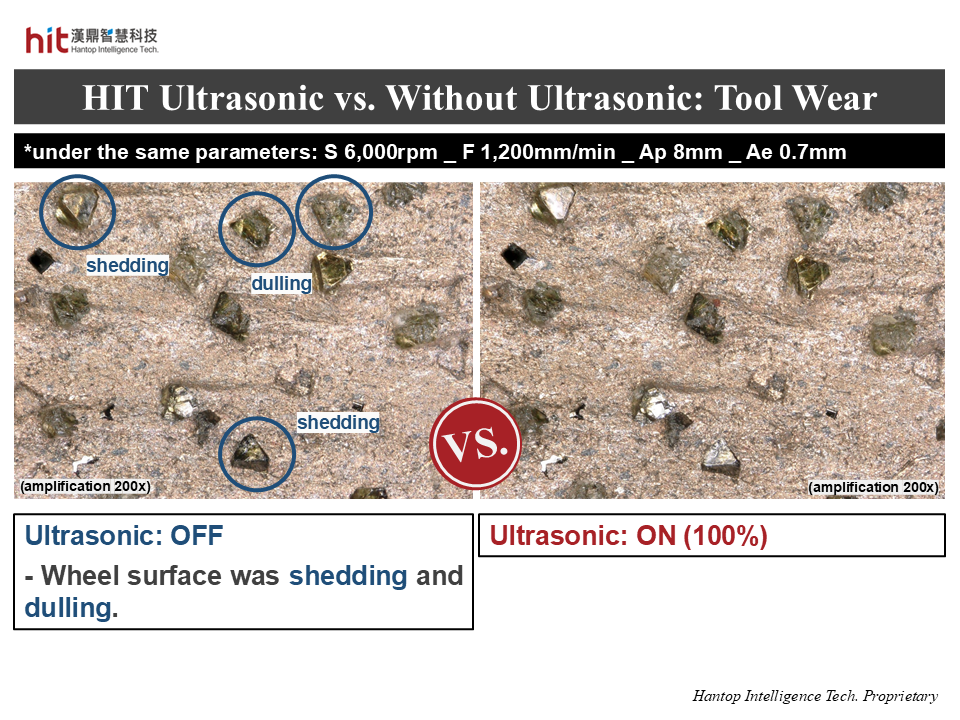
(Figure 7. with HIT new product HBT-40 ultrasonic grinding wheel toolholder module, it helped greatly reduce tool wear compared to that without ultrasonic)
- To optimize the (rough) side grinding process of quartz glass with HIT ultrasonic module, the high frequency micro-vibration helped reduce grinding force.
- Under 2x higher efficiency, the wheel surface only appeared to have mild wear with stable workpiece quality. However, under the same parameters, the wheel surface was shedding and dulling without ultrasonic. This resulted in unstable workpiece quality.
HIT Ultrasonic Machining Technology Achievements in (Rough) Side Grinding of Quartz Glass with D100-Grinding Wheel Toolholder
(with HIT HBT40 Ultrasonic Grinding Wheel Toolholder)
🕜 Efficiency - 2x higher, and nearly 3x higher MRR
📈 Quality - 1.5x better
⚙️ Tool Life - greatly reduced tool wear