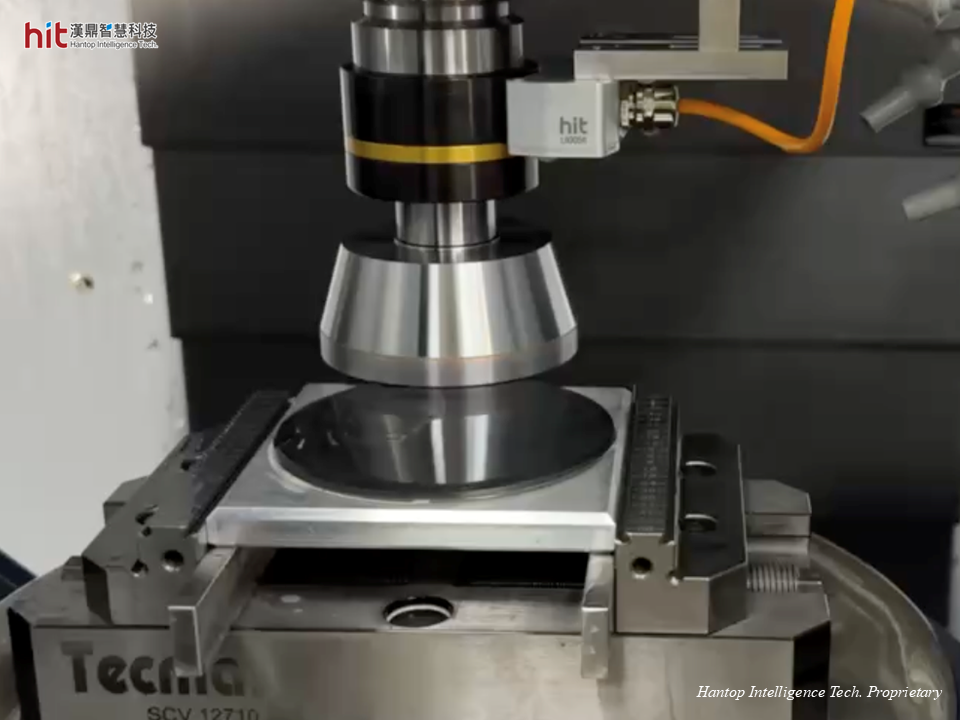
(Figure 1. HIT HBT-40 ultrasonic grinding wheel toolholder module was used on surface grinding of silicon carbide ceramic)
HIT's Goal in Surface Grinding of Silicon Carbide (SiC) with D100-Grinding Wheel Toolholder
Through the assistance of HIT ultrasonic-assisted machining technology with the new product - Ultrasonic Grinding Wheel Toolholder, the goal is to enhance workpiece quality and tool life.
Ultrasonic-Assisted Surface Grinding of Silicon Carbide (SiC) with D100-Grinding Wheel Toolholder: Machining Results
Surface Grinding of Silicon Carbide (SiC) with D100-Grinding Wheel Toolholder: Machining Efficiency
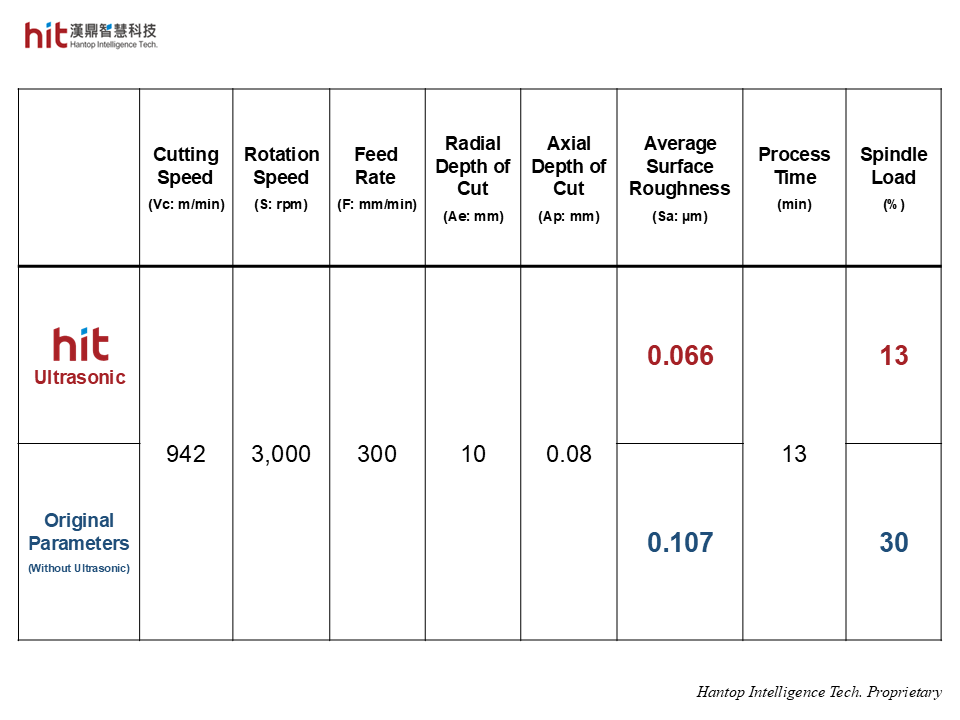
(Figure 2. with HIT new product HBT-40 ultrasonic grinding wheel toolholder module in surface grinding of silicon carbide, it not only enhanced surface quality of workpiece but also lowered spindle load)
- To optimize the surface grinding process of silicon carbide (SiC) with HIT ultrasonic module, the high frequency micro-vibration helped reduce grinding force.
- The 2.3x lower spindle load (from 30% down to 13%) reflected on the reduction in grinding force.
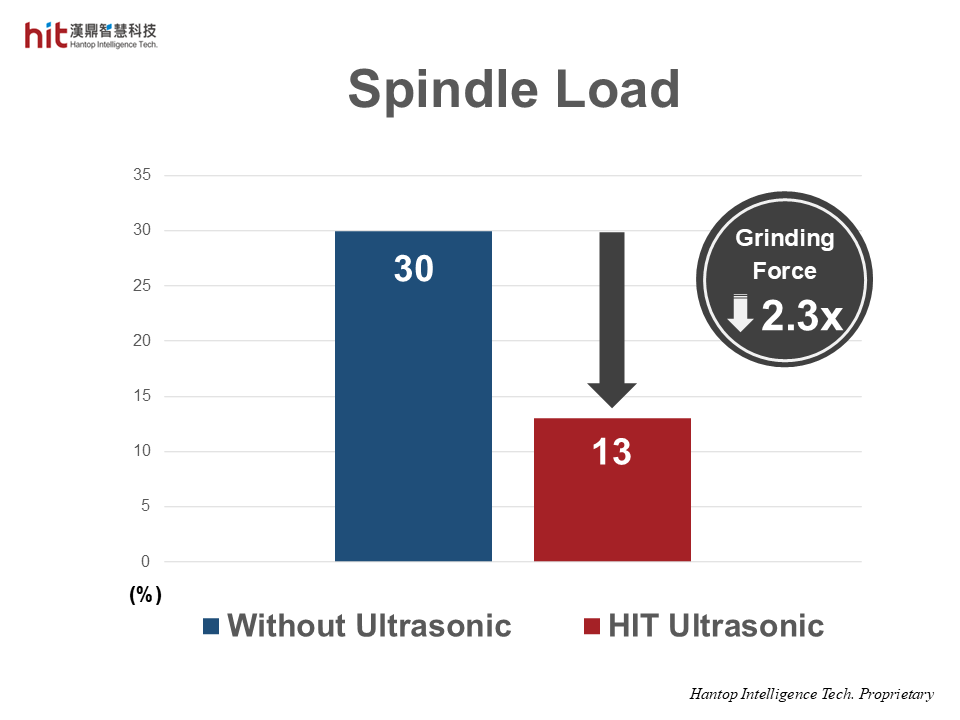
(Figure 3. with HIT new product HBT-40 ultrasonic grinding wheel toolholder module in surface grinding of silicon carbide, 2.3x lower spindle load reflected on the reduction in grinding force)
Surface Grinding of Silicon Carbide (SiC) with D100-Grinding Wheel Toolholder: Surface Quality
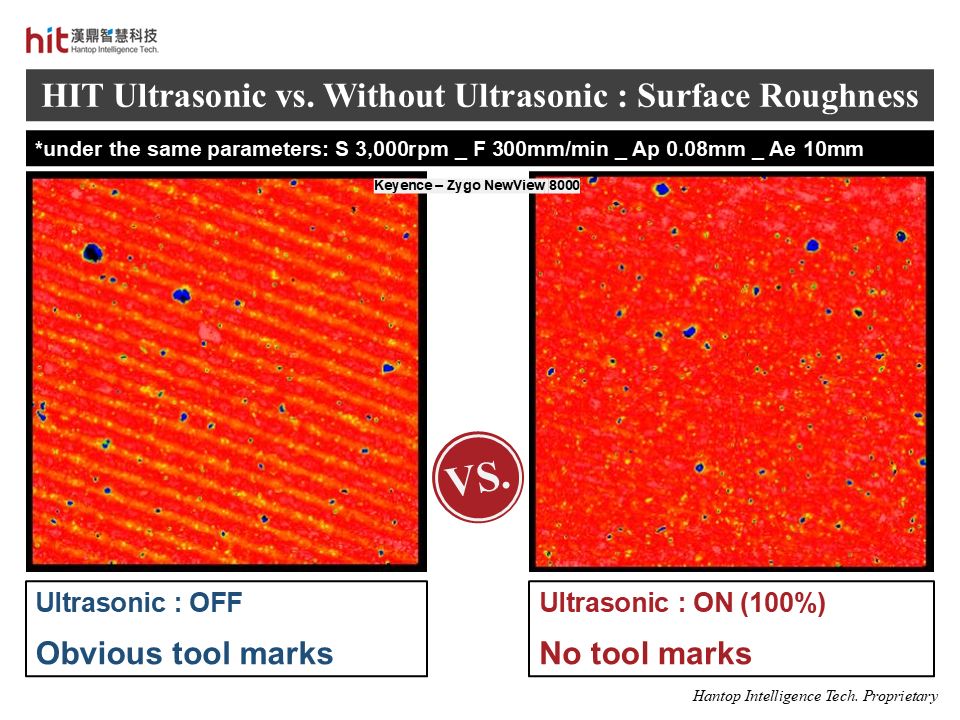
(Figure 4. with HIT new product HBT-40 ultrasonic grinding wheel toolholder module in surface grinding of silicon carbide, it helped remove tool marks on the surface of workpiece)
- To optimize the surface grinding process of silicon carbide (SiC) with HIT ultrasonic module, the high frequency micro-vibration helped reduce grinding force. This can be seen on the reduction in spindle load.
- In addition to 1.6x lower average surface roughness (Sa), the overall surface quality was improved with no tool marks on the surface.
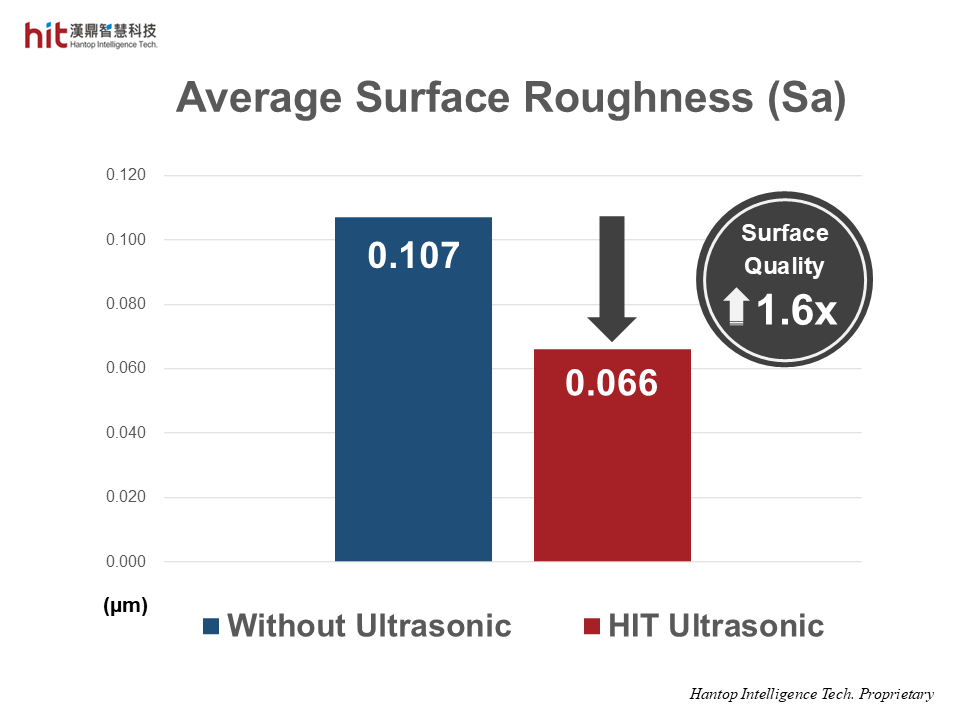
(Figure 5. with HIT new product HBT-40 ultrasonic grinding wheel toolholder module in surface grinding of silicon carbide, the average surface roughness was improved, which brought 1.6x better surface quality)
Surface Grinding of Silicon Carbide (SiC) with D100-Grinding Wheel Toolholder: Tool Life
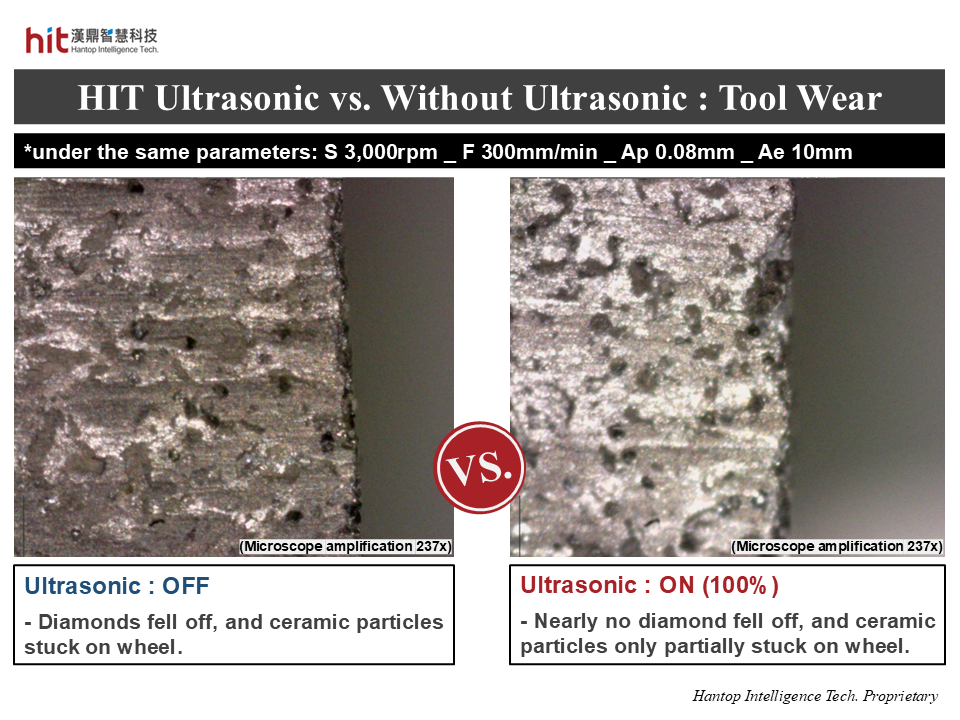
(Figure 6. with HIT new product HBT-40 ultrasonic grinding wheel toolholder module in surface grinding of silicon carbide, tool wear could be greatly reduced compared to that without ultrasonic)
- To optimize the surface grinding process of silicon carbide (SiC) with HIT ultrasonic module, the reduction in grinding force not only brought much lower spindle load and improved surface quality but also helped reduce cutting heat, which prolonged the grinding ability of the wheel.
- The high frequency micro-vibration of ultrasonic also provided better ceramic particles flushing mechanism. As a result, ceramic particles were only partially stuck on the wheel surface.
HIT Ultrasonic Machining Technology Achievements in Surface Grinding of Silicon Carbide (SiC) with D100-Grinding Wheel Toolholder
(with HIT HBT40 Ultrasonic Grinding Wheel Toolholder)
🕜 Spindle Load - 2.3x lower, reflecting on the reduction in grinding force
📈 Surface Quality - 1.6x better, with no tool marks
⚙️ Tool Life - greatly reduced tool wear